Soybean oil Production From Cleaning, Drying, and Dehulling
Production Cost Report | Agriculture, Farming and Commodity
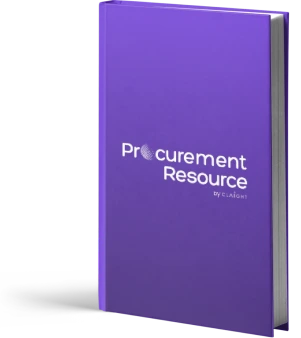
Details: Germany - based plant Q1 2025 | From $ USD
This report consists of a detailed cost analysis of Soybean Oil from Cleaning, Drying, and Dehulling. Before the oil is extracted, the soybeans are cleaned, dried, and dehulled. Because they absorb oil and result in a lesser yield, the soybean hulls must be removed. By splitting the soybeans and mechanically separating the hulls and cracked soybeans, the hulls are removed during this de-hulling process. In order to facilitate oil extraction, the soybeans are also heated to a temperature of about 75 °C to coagulate the soy proteins.
The soybeans are then divided into flakes and placed in percolation extractors where they are mixed with a solvent, often hexane. Evaporators are used to extract the hexane from the soybean oil. Hexane that has evaporated is collected and added back to the extraction procedure. The crude soybean oil without hexane is then further refined.
The crude soybean oil still needs to be cleaned off several oil-soluble and oil-insoluble contaminants. Filtering is used to remove the oil-insoluble materials, and various processes are used to remove the soluble materials, such as degumming (the removal of phosphatides), oil refining (washing with an alkaline solution to remove free fatty acids, colourants, insoluble matter, and gums), and bleaching (using activated earth or activated carbon to remove colour and other impurities).
The project economic analysis provided in the report discusses a Germany-based plant:
- Manufacturing Process
- Process Flow
- Material Flow
- Material Balance
- Raw Material and Product's Specifications
- Raw Material Consumption
- Product and Co-Product Generation
- Capital Investment
- Land and Site Cost
- Offsites/Civil Works
- Equipment Cost
- Auxiliary Equipment Cost
- Contingency
- Engineering and Consulting Charges
- Working Capital
- Variable Cost
- Raw Material
- Utilities
- Fixed Cost
- Labor Requirement & Wages
- Overhead Expenses
- Maintenance Charges
- Financing Costs
- Interest on Working Capital
- Interest on Loans
- Depreciation Charges
- General Sales and Admin Costs
- Production Cost Summary
Report Content
Key Process Information
Evaluation of significant technical parameters along with process descriptions such as:
- Consumption of Raw Material
- Product Creation
- Block Flow Diagram
- Description of the Manufacturing Facility
Utilities Consumption
Evaluation of utilities consumed during the entire process based on:
- Consumption per unit of product generated
- Utility cost split and share of each utility in the total cost
Process Flow Diagram
Representation of various operations involved including:
- Step-wise process
- Utility consumption in each operation
Capital Cost Analysis
In-depth analysis of costs involved in setting up a new manufacturing unit, including:
- Cost of Building a Process Unit
- Cost of Setting Up the Infrastructure
- Working Capital
- Commissioning & Start-Up of the Plant
Implementation Schedule
Time frame of the project design, which includes:
- Plant Start-Up
- Plant Construction
- Engineering Fundamentals
- Raw Material Procurement
Construction Cost Details
Detailed analysis of costs involved in the operation of various functional units in the process unit and infrastructure.
Operating Cost Analysis
Evaluation of costs associated with the production of the final product, namely:
- Procurement of Raw Materials
- Consumption of Utilities
- Fixed Costs
- Depreciation
Economic Analysis
Analysis of the way in which process economics are impacted by plant capacity.
- Construction Cost
- Working Capital
- Fixed and Variable Operating Costs
- Corporate Overhead
- Depreciation
Customized Analyses
Detailed cost estimates of any industrial plant depending on your requirements, including plant capacity and location as per the need.
Compare & Choose the Right Report Version for You

You can easily get a quote for any Procurement Resource report. Just click here and raise a request. We will get back to you within 24 hours. Alternatively, you can also drop us an email at sales@procurementresource.com.
RIGHT PEOPLE
At Procurement Resource our analysts are selected after they are assessed thoroughly on having required qualities so that they can work effectively and productively and are able to execute projects based on the expectations shared by our clients. Our team is hence, technically exceptional, strategic, pragmatic, well experienced and competent.
RIGHT METHODOLOGY
We understand the cruciality of high-quality assessments that are important for our clients to take timely decisions and plan strategically. We have been continuously upgrading our tools and resources over the past years to become useful partners for our clientele. Our research methods are supported by most recent technology, our trusted and verified databases that are modified as per the needs help us serve our clients effectively every time and puts them ahead of their competitors.
RIGHT PRICE
Our team provides a detailed, high quality and deeply researched evaluations in competitive prices, that are unmatchable, and demonstrates our understanding of our client’s resource composition. These reports support our clientele make important procurement and supply chains choices that further helps them to place themselves ahead of their counterparts. We also offer attractive discounts or rebates on our forth coming reports.
RIGHT SUPPORT
Our vision is to enable our clients with superior quality market assessment and actionable evaluations to assist them with taking timely and right decisions. We are always ready to deliver our clients with maximum results by delivering them with customised suggestions to meet their exact needs within the specified timeline and help them understand the market dynamics in a better way.
SELECT YOUR LICENCE TYPE
- Review the available license options and choose the one that best fits your needs. Different licenses offer varying levels of access and usage rights, so make sure to pick the one that aligns with your requirements.
- If you're unsure which license is right for you, feel free to contact us for assistance.
CLICK 'BUY NOW'
- Once you've selected your desired report and license, click the ‘Buy Now’ button. This will add the report to your cart. You will be directed to the registration page where you’ll provide the necessary information to complete the purchase.
- You’ll have the chance to review your order and make adjustments, including updating your license or quantity, before proceeding to the next step.
COMPLETE REGISTRATION
- Enter your details for registration. This will include your name, email address, and any other necessary information. Creating an account allows you to easily manage your orders and gain access to future purchases or reports.
- If you already have an account with us, simply log in to streamline the process.
CHOOSE YOUR PAYMENT METHOD
- Select from a variety of secure payment options, including credit/debit cards, PayPal, or other available gateways. We ensure that all transactions are encrypted and processed securely.
- After selecting your payment method, you will be redirected to a secure checkout page to complete your transaction.
CONFIRM YOUR PURCHASE
- Once your payment is processed, you will receive an order confirmation email from sales@procurementresource.com confirming the dedicated project manger and delivery timelines.
ACCESS YOUR REPORT
- The report will be delivered to you by the project manager within the specified timeline.
- If you encounter any issues accessing your report, project manager would remain connected throughout the length of the project. The team shall assist you with post purchase analyst support for any queries or concerns from the deliverable (within the remit of the agreed scope of work).