Prefeasibility Reports
Check Our Reports - Search by Industrial Product
Try: Ethylene, Butadiene, BD, Propene
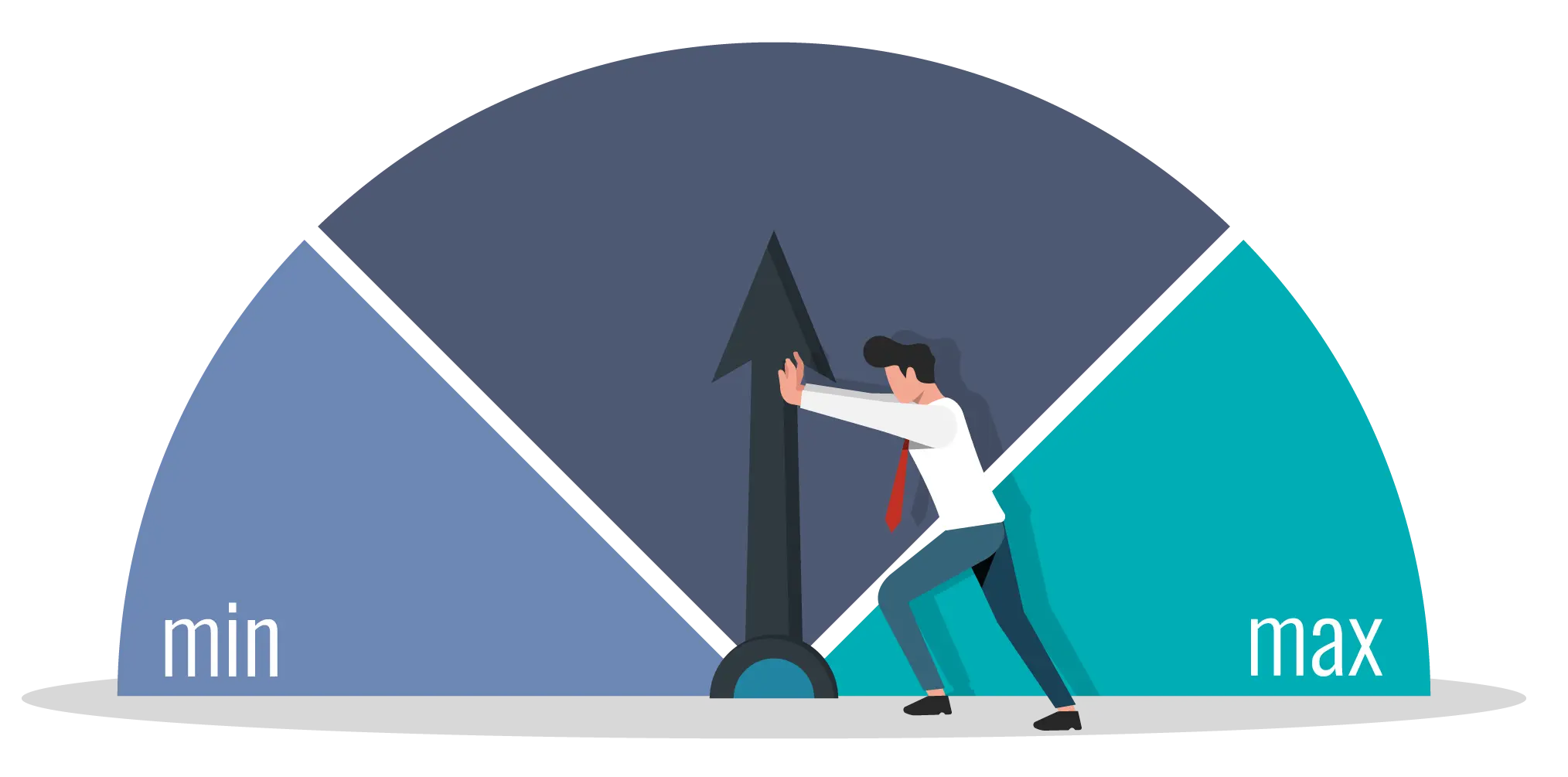
Production Cost Reports | Prefeasibility Reports
Reports Examining Production Processes, Capital & Operating Costs and all Techno Economic Parameters
Key Process Information
Evaluation of significant technical parameters along with process descriptions such as:
- Consumption of Raw Material
- Product Creation
- Block Flow Diagram
- Description of the Manufacturing Facility
Utilities Consumption
Evaluation of utilities consumed during the entire process based on:
- Consumption per unit of product generated
- Utility cost split and share of each utility in the total cost
Process Flow Diagram
Representation of various operations involved including:
- Step-wise process
- Utility consumption in each operation
Capital Cost Analysis
In-depth analysis of costs involved in setting up a new manufacturing unit, including:
- Cost of Building a Process Unit
- Cost of Setting Up the Infrastructure
- Working Capital
- Commissioning & Start-Up of the Plant
Implementation Schedule
Time frame of the project design, which includes:
- Plant Start-Up
- Plant Construction
- Engineering Fundamentals
- Raw Material Procurement
Construction Cost Details
Detailed analysis of costs involved in the operation of various functional units in the process unit and infrastructure.
Operating Cost Analysis
Evaluation of costs associated with the production of the final product, namely:
- Procurement of Raw Materials
- Consumption of Utilities
- Fixed Costs
- Depreciation
Economic Analysis
Analysis of the way in which process economics are impacted by plant capacity.
- Construction Cost
- Working Capital
- Fixed and Variable Operating Costs
- Corporate Overhead
- Depreciation
Customized Analyses
Detailed cost estimates of any industrial plant depending on your requirements, including plant capacity and location as per the need.
Trusted By Leaders
Our valuable insights have helped companies across various sectors all over the world, enabling us to gain the trust and confidence of large MNCs.
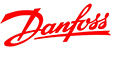
Danfoss
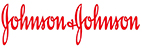
Johnson and Johnson

Unilever

Diversey
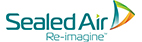
Sealed Air
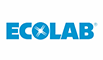
Ecolab

HP

Jeenan Investment
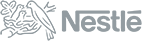