Acrylonitrile Butadiene Styrene (ABS) Production Cost Reports
Chemicals
The report provides a detailed analysis essential for establishing an Acrylonitrile Butadiene Styrene (ABS) manufacturing plant. It encompasses all critical aspects necessary for Acrylonitrile Butadiene Styrene (ABS) production, including the cost of Acrylonitrile Butadiene Styrene (ABS) production, Acrylonitrile Butadiene Styrene (ABS) plant cost, Acrylonitrile Butadiene Styrene (ABS) production costs, and the overall Acrylonitrile Butadiene Styrene (ABS) manufacturing plant cost. Additionally, the study covers specific expenditures associated with setting up and operating an Acrylonitrile Butadiene Styrene (ABS) production plant. These encompass manufacturing processes, raw material requirements, utility requirements, infrastructure needs, machinery and technology requirements, manpower requirements, packaging requirements, transportation requirements, and more.
Acrylonitrile Butadiene Styrene, commonly known as ABS, is a sturdy plastic used to make things like LEGO bricks, automotive parts, and electronic housings. It combines strength, glossiness, and toughness, making it ideal for industrial products. The Acrylonitrile Butadiene Styrene (ABS) market is being propelled by the polymer's various applications. It is used in producing products such as auto parts, pipe fittings, electronic housings, consumer products, and Lego toys. It is a standard thermoplastic polymer usually employed in injection moulding applications.
Furthermore, it finds application in making computer keyboard components, plastic face guards for sockets, and protective headgear like hard hats and helmets. In the automotive industry, it is used in items like plastic alloys and decorative interior components of automobiles. In the construction industry, it finds usage for manufacturing plastic tubing and corrugated plastic structures. Other products that use the polymer, furthering its industrial demand, are printers, vacuum cleaners, musical instruments, utensils, and faxes, along with its growing employment in 3D printing as it can be easily moulded, electroplated, etc.
The main driver of the ABS market is its extensive use as automotive components, household appliances, electronic appliances like computer keyboard parts, and consumer goods for automobile, electrical, and packed goods industries. The other big element driving up the demand for ABS is the construction and medical industry for its usage in the manufacture of pipe fittings, insulin pens, and respiratory devices, respectively. It is a popular engineering plastic owing to its low cost and easy to work with property, which further promotes its market growth. Therefore, due to high demand, there is a greater outflow in the cost of producing ABS. Moreover, the availability and cost of production of ABS feedstock, ABS market prices, distribution (including trading and shipping), logistics, etc., are some of the elements that influence an industrial ABS procurement.
Raw Material for Acrylonitrile Butadiene Styrene (ABS) Production
According to the ABS manufacturing plant project report, the major raw materials for ABS production include Acrylonitrile-Styrene; Butadiene-Acrylonitrile
Manufacturing Process of Acrylonitrile Butadiene Styrene (ABS)
The extensive ABS production cost report consists of this major industrial manufacturing process:
- Production via Mass Process: In this procedure, a mill is used to process butadiene rubber. Acrylonitrile and styrene are combined in this same mill. Then, copolymerization is carried out in two phases, in the presence of a solvent. A devolatilization phase is added to the produced resin to recover and recycle the monomers. After then, ABS is derived.
- Production via Emulsion Polymerization Process: The ABS emulsion polymerization process is the method used to create Acrylonitrile Butadiene Styrene. Under the influence of water, this process turns butadiene into latex. Graft latex is then made using acrylonitrile and styrene monomers. ABS is finally removed from this by filtering.
Acrylonitrile Butadiene Styrene (ABS) is an engineering thermoplastic & amorphous polymer. It comprises of three monomers: acrylonitrile (the synthetic monomer made using propylene and ammonia), butadiene (formed as a by-product of ethylene production from steam crackers), and styrene (made using the dehydrogenation of ethyl benzene). It is available in grades including high and medium impact, high heat resistance, and electroplatable.
The polymer has physical properties like being impact-resistant, high rigidity, anti-strain and abrasion, excellent insulating properties, great weldability, high dimensional stability and surface brightness and excellent surface aspect. In addition, it is resistant to diluted acid and alkalis and shows moderate resistance to aliphatic hydrocarbons and weak resistance to aromatic hydrocarbons, halogenated hydrocarbons, as well as alcohols.
Acrylonitrile Butadiene Styrene (ABS) Production Cost Processes with Cost Analysis
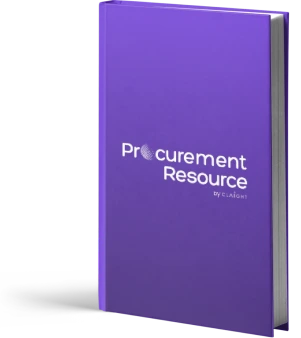
Acrylonitrile Butadiene Styrene Production via mass process
In this process butadiene rubber is processed in a mill. In this same mill acrylonitrile and styrene are mixed.
Details: Germany - based plant Q1 2025 From $ 2499.00 USD
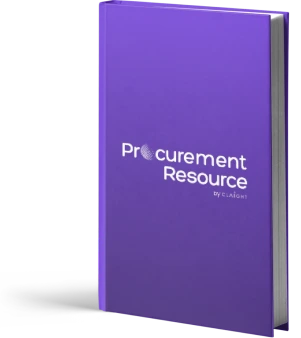
Acrylonitrile Butadiene Styrene Production from Emulsion polymerization process
This process to produce Acrylonitrile Butadiene Styrene is called the ABS emulsion polymerization process.
Details: Germany - based plant Q1 2025 From $ 2499.00 USD
Product Details
Particulars | Details |
---|---|
Product Name | Acrylonitrile Butadiene Styrene (ABS) |
Scope | Manufacturing Process: Process Flow, Material Flow, Material Balance Raw Material and Product Specifications: Raw Material Consumption, Product and Co-product Generation Land and Site Cost: Offsites/Civil Works, Equipment Cost, Auxiliary Equipment Costs, Contingency, Engineering and Consulting Charges, Working Capital Variable Cost: Raw Material, Utilities, Other Variable Costs Fixed Cost: Labor Requirements and Wages, Overhead Expenses, Maintenance Charges, and Other Fixed Costs Financing Costs: Interest on Working Capital, Interest on Loans Other Costs: Depreciation Charges, General Sales, and Admin Cost |
Currency | US$ (Data can also be provided in the local currency) |
Pricing and Purchase Options | Basic: US$ 2499 Premium: US$ 3499 Enterprise: US$ 4799 |
Customization Scope | The report can be customized as per the requirement of the customer |
Post-Sale Analysts Report | 10-12 weeks of post-purchase analyst support after report delivery for any queries from the deliverable |
Delivery Format | PDF and Excel format through email (editable version in PPT/Word format of the report can be also provided on special request) |
How does our Acrylonitrile Butadiene Styrene (ABS) Production Cost Report Provide Exhaustive Data and Extensive Insights?
At Procurement Resource, we not only focus on optimizing the should cost of production for Acrylonitrile Butadiene Styrene (ABS) but also provide our clients with extensive intel and rigorous information on every aspect of the production process. By utilizing a comprehensive cost model, we help you break down expenses related to raw materials, labor, and technology, offering clear pathways to savings. We also assist in evaluating the capital expenditure (CAPEX) and operating expenses (OPEX), which are often measured as cost per unit of production, such as USD/MT, ensuring that your financial planning is aligned with industry benchmarks.
We offer valuable insights on the top technology providers, in-depth supplier database, and best manufacturers, helping you make informed decisions to improve efficiency. Additionally, we design the most feasible layout for your production needs, ensuring the entire process runs smoothly. By minimizing the cash cost of production, we ensure that you stay competitive while securing long-term profitability in the growing Acrylonitrile Butadiene Styrene (ABS) market. Partnering with Procurement Resource guarantees that every aspect of your production is cost-efficient, advanced, and tailored to your specific requirements.
Key Questions Answered in This Report
- What are the key requirements for setting up an Acrylonitrile Butadiene Styrene (ABS) manufacturing plant?
- How is Acrylonitrile Butadiene Styrene (ABS) manufactured?
- What is the process flow involved in producing Acrylonitrile Butadiene Styrene (ABS)?
- What are the raw material requirements and costs for producing Acrylonitrile Butadiene Styrene (ABS)?
- What is the total size of land required for setting up an Acrylonitrile Butadiene Styrene (ABS) manufacturing plant?
- What are the construction requirements for setting up an Acrylonitrile Butadiene Styrene (ABS) manufacturing plant?
- What are the machinery requirements for producing Acrylonitrile Butadiene Styrene (ABS)?
- What are the utility requirements and costs for producing Acrylonitrile Butadiene Styrene (ABS)?
- What are the manpower requirements for producing Acrylonitrile Butadiene Styrene (ABS)?
- What are the average salaries/wages of manpower working in an Acrylonitrile Butadiene Styrene (ABS) manufacturing plant?
- What are the packaging requirements and associated costs for Acrylonitrile Butadiene Styrene (ABS)?
- What are the transportation requirements and associated costs for Acrylonitrile Butadiene Styrene (ABS)?
- What are the capital costs for setting up an Acrylonitrile Butadiene Styrene (ABS) manufacturing plant?
- What are the operating costs for setting up an Acrylonitrile Butadiene Styrene (ABS) manufacturing plant?
- What should be the price of Acrylonitrile Butadiene Styrene (ABS)?
- What will be the income and expenditures for an Acrylonitrile Butadiene Styrene (ABS) manufacturing plant?
Need more help?
- We can tailor the report as per your unique requirements such as desired capacity, future expansion plans, product specifications, mode of financing, plant location, etc.
- We can also provide a flexible, easy-to-use, dynamic excel-based cost-model/ dashboard where you can change the inputs to get different outputs
- Speak to our highly skilled team of analysts for insights on the recent trends and innovations, industry best practices, key success and risk factors, product pricing, margins, return on investment, industry standards and regulations, etc.
- Gain an unparalleled competitive advantage in your domain by understanding how to optimize your business operations and maximize profits
- For further assistance, please connect with our analysts
Compare & Choose the Right Report Version for You

You can easily get a quote for any Procurement Resource report. Just click here and raise a request. We will get back to you within 24 hours. Alternatively, you can also drop us an email at sales@procurementresource.com.
RIGHT PEOPLE
At Procurement Resource our analysts are selected after they are assessed thoroughly on having required qualities so that they can work effectively and productively and are able to execute projects based on the expectations shared by our clients. Our team is hence, technically exceptional, strategic, pragmatic, well experienced and competent.
RIGHT METHODOLOGY
We understand the cruciality of high-quality assessments that are important for our clients to take timely decisions and plan strategically. We have been continuously upgrading our tools and resources over the past years to become useful partners for our clientele. Our research methods are supported by most recent technology, our trusted and verified databases that are modified as per the needs help us serve our clients effectively every time and puts them ahead of their competitors.
RIGHT PRICE
Our team provides a detailed, high quality and deeply researched evaluations in competitive prices, that are unmatchable, and demonstrates our understanding of our client’s resource composition. These reports support our clientele make important procurement and supply chains choices that further helps them to place themselves ahead of their counterparts. We also offer attractive discounts or rebates on our forth coming reports.
RIGHT SUPPORT
Our vision is to enable our clients with superior quality market assessment and actionable evaluations to assist them with taking timely and right decisions. We are always ready to deliver our clients with maximum results by delivering them with customised suggestions to meet their exact needs within the specified timeline and help them understand the market dynamics in a better way.
SELECT YOUR LICENCE TYPE
- Review the available license options and choose the one that best fits your needs. Different licenses offer varying levels of access and usage rights, so make sure to pick the one that aligns with your requirements.
- If you're unsure which license is right for you, feel free to contact us for assistance.
CLICK 'BUY NOW'
- Once you've selected your desired report and license, click the ‘Buy Now’ button. This will add the report to your cart. You will be directed to the registration page where you’ll provide the necessary information to complete the purchase.
- You’ll have the chance to review your order and make adjustments, including updating your license or quantity, before proceeding to the next step.
COMPLETE REGISTRATION
- Enter your details for registration. This will include your name, email address, and any other necessary information. Creating an account allows you to easily manage your orders and gain access to future purchases or reports.
- If you already have an account with us, simply log in to streamline the process.
CHOOSE YOUR PAYMENT METHOD
- Select from a variety of secure payment options, including credit/debit cards, PayPal, or other available gateways. We ensure that all transactions are encrypted and processed securely.
- After selecting your payment method, you will be redirected to a secure checkout page to complete your transaction.
CONFIRM YOUR PURCHASE
- Once your payment is processed, you will receive an order confirmation email from sales@procurementresource.com confirming the dedicated project manger and delivery timelines.
ACCESS YOUR REPORT
- The report will be delivered to you by the project manager within the specified timeline.
- If you encounter any issues accessing your report, project manager would remain connected throughout the length of the project. The team shall assist you with post purchase analyst support for any queries or concerns from the deliverable (within the remit of the agreed scope of work).