Frozen Vegetables Production Cost Reports
Food and Beverages
The report provides a detailed production cost analysis for frozen vegetables. It encompasses all critical aspects necessary for frozen vegetables production, including the cost of frozen vegetables production, frozen vegetables production cost model, and other extensive details. These encompass production processes, raw material requirements, utility requirements, infrastructure needs, machinery and technology requirements, manpower requirements, packaging requirements, transportation requirements, and more.
Frozen vegetables are preserved vegetables that are produced by treating the fresh vegetables through blanching and then quick freezing. These vegetables are naturally preserved, consisting of their natural nutrients and having longer shelf-life. It is largely associated with the food production units, where these are included as natural ingredients in packaged and processed food varieties. Frozen vegetables are used to add that fresh look to the prepared delicacy.
The vegetables add color, freshness, and nutrients to the food product. It is used to produce ready-to-eat food varieties, including instant soup, noodles, and other packaged varieties. Moreover, frozen vegetables serve as ingredients in stews, toppings, etc., and can be added to a variety of dishes, including curries, pizza, pasta, fries, etc.
The Frozen Vegetables market is being driven by factors like rapid urbanisation, growing disposable income, and an increasing shift towards ready-to-eat foods. Furthermore, growing developments in technology paired with easy storage, aesthetic packaging, and general availability of the product are furthering its demand.
In addition, the growing number of the working population that prefers stored and instant foods is another factor contributing to the industry's expansion. Also, th e rising preference for low-fat and high-protein vegetables as part of the diet among consumers is boosting the market expansion. Its demand as a food ingredient in ready-to-eat products contributes towards strengthening its market growth.
Its demand in the food industry plays a vital role and influences the industrial frozen vegetable procurement in the global market. Hence, the shifts in its demand, along with some other factors, including its market prices, production, etc., are highly essential for its procurement across various regions.
Raw Material for Frozen Vegetables Production
According to the frozen vegetables production cost report, the key raw material for frozen vegetables production includes liquid nitrogen (for quick freezing), hot water for blanching, cold/ice water for shocking, ice, packaging materials, freezing equipment, a timer, and blanching baskets.
Production Process of Frozen Vegetables
The extensive frozen vegetables production cost report consists of the following industrial production process:
- By Blanching and Quick Freezing: The production process of frozen vegetables in initiated by treating the required vegetable through blanching in hot water. The process is followed by quickly freezing the vegetables and locking their natural nutrient content. The treated vegetables are then processed for packaging and supply.
Frozen Vegetables are vegetables that are frozen right after a few hours of being picked and thawed. The frozen products can be heated in a microwave and can be prepared and consumed. Presently, vegetables are frozen by the freezing process. At first, raw vegetables are checked for their quality, whereas bad vegetables are removed. After the selection process, the vegetables are cleaned and peeled.
These vegetables get blanched via boiling in hot water. This process is carried out carefully to stop the action of enzymes and preserve their color, taste, and texture. The vegetables are then packed and processed for freezing prior to being sold as frozen vegetables.
Frozen Vegetables are fresh in taste and texture and offer great convenience. These vegetables are preserved; hence, their nutritional content also stays intact, making them a rich source of vitamins (A, C, and folate), minerals (potassium, calcium, iron), fiber, phytochemicals, or compounds found in plants, like polyphenols and flavonoids and antioxidants.
Frozen Vegetables Production Cost Processes with Cost Analysis
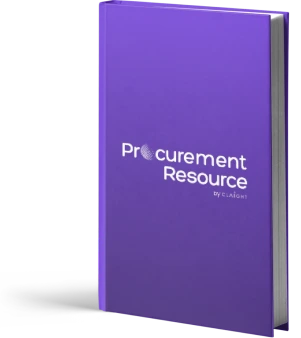
Frozen Vegetables Production from Blanching and Freezing
This report provides the cost structure of the production of frozen vegetables from the freezing process. Raw vegetables go through a quality check process where any bad quality vegetables are removed.
Details: Germany - based plant Q1 2025 From $ 2499.00 USD
Product Details
Particulars | Details |
---|---|
Product Name | Frozen Vegetables |
Scope | Manufacturing Process: Process Flow, Material Flow, Material Balance Raw Material and Product Specifications: Raw Material Consumption, Product and Co-product Generation Land and Site Cost: Offsites/Civil Works, Equipment Cost, Auxiliary Equipment Costs, Contingency, Engineering and Consulting Charges, Working Capital Variable Cost: Raw Material, Utilities, Other Variable Costs Fixed Cost: Labor Requirements and Wages, Overhead Expenses, Maintenance Charges, Other Fixed Costs Financing Costs: Interest on Working Capital, Interest on Loans Other Costs: Depreciation Charges, General Sales and Admin Cost |
Currency | US$ (Data can also be provided in the local currency) |
Pricing and Purchase Options | Basic: US$ 2499 Premium: US$ 3499 Enterprise: US$ 4799 |
Customization Scope | The report can be customized as per the requirement of the customer |
Post-Sale Analysts Report | 10-12 weeks of post-purchase analyst support after report delivery for any queries from the deliverable |
Delivery Format | PDF and Excel format through email (editable version in PPT/Word format of the report can be also provided on special request) |
How does our Frozen Vegetables Production Cost Report Provide Exhaustive Data and Extensive Insights?
At Procurement Resource, we not only focus on optimizing the should cost of production for Frozen Vegetables but also provide our clients with extensive intel and rigorous information on every aspect of the production process. By utilizing a comprehensive cost model, we help you break down expenses related to raw materials, labor, and technology, offering clear pathways to savings. We also assist in evaluating the capital expenditure (CAPEX) and operating expenses (OPEX), which are often measured as cost per unit of production, such as USD/MT, ensuring that your financial planning is aligned with industry benchmarks.
We offer valuable insights on the top technology providers, in-depth supplier database, and best manufacturers, helping you make informed decisions to improve efficiency. Additionally, we design the most feasible layout for your production needs, ensuring the entire process runs smoothly. By minimizing the cash cost of production, we ensure that you stay competitive while securing long-term profitability in the growing Frozen Vegetables market. Partnering with Procurement Resource guarantees that every aspect of your production is cost-efficient, advanced, and tailored to your specific requirements.
Key Questions Answered in This Report
- What are the key requirements for setting up a Frozen Vegetables manufacturing plant?
- How is Frozen Vegetables manufactured?
- What is the process flow involved in producing Frozen Vegetables?
- What are the raw material requirements and costs for producing Frozen Vegetables?
- What is the total size of land required for setting up a Frozen Vegetables manufacturing plant?
- What are the construction requirements for setting up a Frozen Vegetables manufacturing plant?
- What are the machinery requirements for producing Frozen Vegetables?
- What are the utility requirements and costs for producing Frozen Vegetables?
- What are the manpower requirements for producing Frozen Vegetables?
- What are the average salaries/wages of manpower working in a Frozen Vegetables manufacturing plant?
- What are the packaging requirements and associated costs for Frozen Vegetables?
- What are the transportation requirements and associated costs for Frozen Vegetables?
- What are the capital costs for setting up a Frozen Vegetables manufacturing plant?
- What are the operating costs for setting up a Frozen Vegetables manufacturing plant?
- What should be the price of Frozen Vegetables?
- What will be the income and expenditures for a Frozen Vegetables manufacturing plant?
Need more help?
- We can tailor the report as per your unique requirements such as desired capacity, future expansion plans, product specifications, mode of financing, plant location, etc.
- We can also provide a flexible, easy-to-use, dynamic excel-based cost-model/ dashboard where you can change the inputs to get different outputs
- Speak to our highly skilled team of analysts for insights on the recent trends and innovations, industry best practices, key success and risk factors, product pricing, margins, return on investment, industry standards and regulations, etc.
- Gain an unparalleled competitive advantage in your domain by understanding how to optimize your business operations and maximize profits
- For further assistance, please connect with our analysts
Compare & Choose the Right Report Version for You

You can easily get a quote for any Procurement Resource report. Just click here and raise a request. We will get back to you within 24 hours. Alternatively, you can also drop us an email at sales@procurementresource.com.
RIGHT PEOPLE
At Procurement Resource our analysts are selected after they are assessed thoroughly on having required qualities so that they can work effectively and productively and are able to execute projects based on the expectations shared by our clients. Our team is hence, technically exceptional, strategic, pragmatic, well experienced and competent.
RIGHT METHODOLOGY
We understand the cruciality of high-quality assessments that are important for our clients to take timely decisions and plan strategically. We have been continuously upgrading our tools and resources over the past years to become useful partners for our clientele. Our research methods are supported by most recent technology, our trusted and verified databases that are modified as per the needs help us serve our clients effectively every time and puts them ahead of their competitors.
RIGHT PRICE
Our team provides a detailed, high quality and deeply researched evaluations in competitive prices, that are unmatchable, and demonstrates our understanding of our client’s resource composition. These reports support our clientele make important procurement and supply chains choices that further helps them to place themselves ahead of their counterparts. We also offer attractive discounts or rebates on our forth coming reports.
RIGHT SUPPORT
Our vision is to enable our clients with superior quality market assessment and actionable evaluations to assist them with taking timely and right decisions. We are always ready to deliver our clients with maximum results by delivering them with customised suggestions to meet their exact needs within the specified timeline and help them understand the market dynamics in a better way.
SELECT YOUR LICENCE TYPE
- Review the available license options and choose the one that best fits your needs. Different licenses offer varying levels of access and usage rights, so make sure to pick the one that aligns with your requirements.
- If you're unsure which license is right for you, feel free to contact us for assistance.
CLICK 'BUY NOW'
- Once you've selected your desired report and license, click the ‘Buy Now’ button. This will add the report to your cart. You will be directed to the registration page where you’ll provide the necessary information to complete the purchase.
- You’ll have the chance to review your order and make adjustments, including updating your license or quantity, before proceeding to the next step.
COMPLETE REGISTRATION
- Enter your details for registration. This will include your name, email address, and any other necessary information. Creating an account allows you to easily manage your orders and gain access to future purchases or reports.
- If you already have an account with us, simply log in to streamline the process.
CHOOSE YOUR PAYMENT METHOD
- Select from a variety of secure payment options, including credit/debit cards, PayPal, or other available gateways. We ensure that all transactions are encrypted and processed securely.
- After selecting your payment method, you will be redirected to a secure checkout page to complete your transaction.
CONFIRM YOUR PURCHASE
- Once your payment is processed, you will receive an order confirmation email from sales@procurementresource.com confirming the dedicated project manger and delivery timelines.
ACCESS YOUR REPORT
- The report will be delivered to you by the project manager within the specified timeline.
- If you encounter any issues accessing your report, project manager would remain connected throughout the length of the project. The team shall assist you with post purchase analyst support for any queries or concerns from the deliverable (within the remit of the agreed scope of work).