MSG (Monosodium Glutamate) Production Cost Reports
Food and Beverages
The report provides a detailed analysis essential for establishing an MSG (Monosodium Glutamate) manufacturing plant. It encompasses all critical aspects necessary for MSG (Monosodium Glutamate) production, including the cost of MSG (Monosodium Glutamate) production, MSG (Monosodium Glutamate) plant cost, MSG (Monosodium Glutamate) production costs, and the overall MSG (Monosodium Glutamate) manufacturing plant cost. Additionally, the study covers specific expenditures associated with setting up and operating an MSG (Monosodium Glutamate) production plant. These encompass manufacturing processes, raw material requirements, utility requirements, infrastructure needs, machinery and technology requirements, manpower requirements, packaging requirements, transportation requirements, and more.
Monosodium Glutamate (MSG) is an organic compound used as a flavor enhancer in the food industry, for its umami taste that provides savory flavors in various dishes. It is commonly found in Asian cuisines, processed foods, canned soups, and snacks like chips and instant noodles. MSG is also utilized in the production of seasoning blends, sauces, and condiments to enhance taste. It allows for reduced sodium content, as it contains only one-third the sodium of table salt. Beyond culinary applications, MSG has some medicinal uses, such as treatment for hepatic coma.
The market for MSG (Monosodium Glutamate) is driven by its usage as a flavor enhancer in processed foods, snacks, soups, and meat products to provide umami flavor, which elevates its demand in the food and beverage industries. The rising consumption of convenience foods and ready-to-eat meals amplifies its market appeal. It serves as a lower-sodium alternative that enhances flavor without increasing salt content, which boosts its demand among health-conscious consumers.
The growth of restaurants and food service establishments also fuels its market demand. Overall, industrial MSG (Monosodium Glutamate) procurement is influenced by its application in the food industry, the availability of its raw materials (natural products like sugarcane and tapioca), the cost of its raw materials, the rising demand for convenience and ready-to-eat foods, lower-sodium alternative, and the growth of food service industry.
Raw Material for MSG (Monosodium Glutamate) Production
According to the MSG (Monosodium Glutamate) manufacturing plant project report, the key raw materials used in the production of MSG (Monosodium Glutamate) include natural products like sugarcane and tapioca.
Manufacturing Process of MSG (Monosodium Glutamate)
The extensive MSG (Monosodium Glutamate) production cost report consists of the following major industrial manufacturing process:
- Production via Bacterial Fermentation: The manufacturing process of MSG (Monosodium Glutamate) starts with the fermentation of natural products like sugarcane and tapioca to obtain glutamic acid. The acid undergoes sodium neutralization to form an MSG solution, followed by the final processes of purification and classification to extract a pure MSG solution.
MSG (Monosodium Glutamate) (C5H8NO4Na) is a well-known and widely used seasoning and flavor booster. It looks like a white crystalline solid that has no odor or smell. It has a molar mass of (anhydrous) 169.11 grams/mole and (a monohydrate) 187.12 grams/mole. Its respective melting and boiling points are 232 °C and 333.8 °C. It has a high solubility in water of around 740 g/l. Its solution has a pH ranging between 6.7 to 7.2. Upon being heated over 232 °C, it decomposes. It acts on the salt receptors and releases neurotransmitters.
MSG (Monosodium Glutamate) Production Cost Processes with Cost Analysis
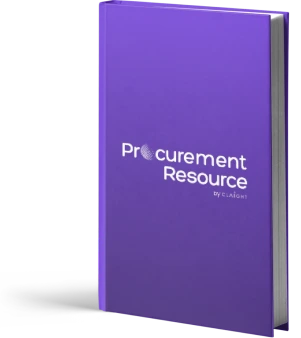
MSG Production from Bacterial Fermentation
This report provides the cost structure of MSG production by the bacterial fermentation method. In this process, natural products like sugarcane and tapioca undergo the process of fermentation to obtain glutamic acid.
Details: Germany - based plant Q1 2025 From $ 2499.00 USD
Product Details
Particulars | Details |
---|---|
Product Name | MSG (Monosodium Glutamate) |
Scope | Manufacturing Process: Process Flow, Material Flow, Material Balance Raw Material and Product Specifications: Raw Material Consumption, Product and Co-product Generation Land and Site Cost: Offsites/Civil Works, Equipment Cost, Auxiliary Equipment Costs, Contingency, Engineering and Consulting Charges, Working Capital Variable Cost: Raw Material, Utilities, Other Variable Costs Fixed Cost: Labor Requirements and Wages, Overhead Expenses, Maintenance Charges, Other Fixed Costs Financing Costs: Interest on Working Capital, Interest on Loans Other Costs: Depreciation Charges, General Sales and Admin Cost |
Currency | US$ (Data can also be provided in the local currency) |
Pricing and Purchase Options | Basic: US$ 2499 Premium: US$ 3499 Enterprise: US$ 4799 |
Customization Scope | The report can be customized as per the requirement of the customer |
Post-Sale Analysts Report | 10-12 weeks of post-purchase analyst support after report delivery for any queries from the deliverable |
Delivery Format | PDF and Excel format through email (editable version in PPT/Word format of the report can be also provided on special request) |
How does our MSG (Monosodium Glutamate) Production Cost Report Provide Exhaustive Data and Extensive Insights?
At Procurement Resource, we not only focus on optimizing the should cost of production for MSG (Monosodium Glutamate) but also provide our clients with extensive intel and rigorous information on every aspect of the production process. By utilizing a comprehensive cost model, we help you break down expenses related to raw materials, labor, and technology, offering clear pathways to savings. We also assist in evaluating the capital expenditure (CAPEX) and operating expenses (OPEX), which are often measured as cost per unit of production, such as USD/MT, ensuring that your financial planning is aligned with industry benchmarks.
We offer valuable insights on the top technology providers, in-depth supplier database, and best manufacturers, helping you make informed decisions to improve efficiency. Additionally, we design the most feasible layout for your production needs, ensuring the entire process runs smoothly. By minimizing the cash cost of production, we ensure that you stay competitive while securing long-term profitability in the growing MSG (Monosodium Glutamate) market. Partnering with Procurement Resource guarantees that every aspect of your production is cost-efficient, advanced, and tailored to your specific requirements.
Key Questions Answered in This Report
- What are the key requirements for setting up an MSG (Monosodium Glutamate) manufacturing plant?
- How is MSG (Monosodium Glutamate) manufactured?
- What is the process flow involved in producing MSG (Monosodium Glutamate)?
- What are the raw material requirements and costs for producing MSG (Monosodium Glutamate)?
- What is the total size of land required for setting up an MSG (Monosodium Glutamate) manufacturing plant?
- What are the construction requirements for setting up an MSG (Monosodium Glutamate) manufacturing plant?
- What are the machinery requirements for producing MSG (Monosodium Glutamate)?
- What are the utility requirements and costs for producing MSG (Monosodium Glutamate)?
- What are the manpower requirements for producing MSG (Monosodium Glutamate)?
- What are the average salaries/wages of manpower working in an MSG (Monosodium Glutamate) manufacturing plant?
- What are the packaging requirements and associated costs for MSG (Monosodium Glutamate)?
- What are the transportation requirements and associated costs for MSG (Monosodium Glutamate)?
- What are the capital costs for setting up an MSG (Monosodium Glutamate) manufacturing plant?
- What are the operating costs for setting up an MSG (Monosodium Glutamate) manufacturing plant?
- What should be the price of MSG (Monosodium Glutamate)?
- What will be the income and expenditures for an MSG (Monosodium Glutamate) manufacturing plant?
Need more help?
- We can tailor the report as per your unique requirements such as desired capacity, future expansion plans, product specifications, mode of financing, plant location, etc.
- We can also provide a flexible, easy-to-use, dynamic excel-based cost-model/ dashboard where you can change the inputs to get different outputs
- Speak to our highly skilled team of analysts for insights on the recent trends and innovations, industry best practices, key success and risk factors, product pricing, margins, return on investment, industry standards and regulations, etc.
- Gain an unparalleled competitive advantage in your domain by understanding how to optimize your business operations and maximize profits
- For further assistance, please connect with our analysts
Compare & Choose the Right Report Version for You

You can easily get a quote for any Procurement Resource report. Just click here and raise a request. We will get back to you within 24 hours. Alternatively, you can also drop us an email at sales@procurementresource.com.
RIGHT PEOPLE
At Procurement Resource our analysts are selected after they are assessed thoroughly on having required qualities so that they can work effectively and productively and are able to execute projects based on the expectations shared by our clients. Our team is hence, technically exceptional, strategic, pragmatic, well experienced and competent.
RIGHT METHODOLOGY
We understand the cruciality of high-quality assessments that are important for our clients to take timely decisions and plan strategically. We have been continuously upgrading our tools and resources over the past years to become useful partners for our clientele. Our research methods are supported by most recent technology, our trusted and verified databases that are modified as per the needs help us serve our clients effectively every time and puts them ahead of their competitors.
RIGHT PRICE
Our team provides a detailed, high quality and deeply researched evaluations in competitive prices, that are unmatchable, and demonstrates our understanding of our client’s resource composition. These reports support our clientele make important procurement and supply chains choices that further helps them to place themselves ahead of their counterparts. We also offer attractive discounts or rebates on our forth coming reports.
RIGHT SUPPORT
Our vision is to enable our clients with superior quality market assessment and actionable evaluations to assist them with taking timely and right decisions. We are always ready to deliver our clients with maximum results by delivering them with customised suggestions to meet their exact needs within the specified timeline and help them understand the market dynamics in a better way.
SELECT YOUR LICENCE TYPE
- Review the available license options and choose the one that best fits your needs. Different licenses offer varying levels of access and usage rights, so make sure to pick the one that aligns with your requirements.
- If you're unsure which license is right for you, feel free to contact us for assistance.
CLICK 'BUY NOW'
- Once you've selected your desired report and license, click the ‘Buy Now’ button. This will add the report to your cart. You will be directed to the registration page where you’ll provide the necessary information to complete the purchase.
- You’ll have the chance to review your order and make adjustments, including updating your license or quantity, before proceeding to the next step.
COMPLETE REGISTRATION
- Enter your details for registration. This will include your name, email address, and any other necessary information. Creating an account allows you to easily manage your orders and gain access to future purchases or reports.
- If you already have an account with us, simply log in to streamline the process.
CHOOSE YOUR PAYMENT METHOD
- Select from a variety of secure payment options, including credit/debit cards, PayPal, or other available gateways. We ensure that all transactions are encrypted and processed securely.
- After selecting your payment method, you will be redirected to a secure checkout page to complete your transaction.
CONFIRM YOUR PURCHASE
- Once your payment is processed, you will receive an order confirmation email from sales@procurementresource.com confirming the dedicated project manger and delivery timelines.
ACCESS YOUR REPORT
- The report will be delivered to you by the project manager within the specified timeline.
- If you encounter any issues accessing your report, project manager would remain connected throughout the length of the project. The team shall assist you with post purchase analyst support for any queries or concerns from the deliverable (within the remit of the agreed scope of work).