Phosgene Production Cost Reports
Chemicals
The report provides a detailed analysis essential for establishing a Phosgene manufacturing plant. It encompasses all critical aspects necessary for Phosgene production, including the cost of Phosgene production, Phosgene plant cost, Phosgene production costs, and the overall Phosgene manufacturing plant cost. Additionally, the study covers specific expenditures associated with setting up and operating a Phosgene production plant. These encompass manufacturing processes, raw material requirements, utility requirements, infrastructure needs, machinery and technology requirements, manpower requirements, packaging requirements, transportation requirements, and more.
Phosgene is a gas that is largely utilized as an intermediary in the manufacture of isocyanates, such as toluene diisocyanate (TDI) and methylene diphenyl diisocyanate (MDI), which are essential to produce polyurethanes and polycarbonate plastics. These materials are widely utilized in everyday products, such as flexible foams for furniture, insulation, coatings, adhesives, and automotive interiors. Additionally, Phosgene plays a role in producing herbicides, pesticides, dyes, and pharmaceutical intermediates.
The market for Phosgene is driven by its usage as an intermediate in the production of various chemicals, mainly in the manufacture of diisocyanates like methylene diphenyl diisocyanate (MDI) and toluene diisocyanate (TDI), which elevates its demand in various industries such as construction, automotive, and furniture industries. Its utilization to synthesize herbicides and pesticides amplifies its demand in the agrochemical industry. Its usage to produce coatings, adhesives, and sealants, as well as specialty chemicals and pharmaceuticals, boosts its demand in the chemical and pharmaceutical industries.
Furthermore, regulations aimed at reducing the use of ozone-depleting substances have increased the demand for Phosgene-based alternatives in the manufacture of certain chemicals, such as refrigerants and blowing agents, which contributes to its demand. Overall, industrial Phosgene procurement is influenced by its application in various industries such as construction, automotive, furniture, agrochemical, chemical, and pharmaceutical industries, the availability of its raw material (chlorine), the cost of its raw material, regulatory approvals, and technological advancements.
Raw Material for Phosgene Production
According to the Phosgene manufacturing plant project report, the key raw material used in the production of Phosgene includes chlorine.
Manufacturing Process of Phosgene
The extensive Phosgene production cost report consists of the following major industrial manufacturing process:
- Production from chlorine: The manufacturing process of Phosgene involves the reaction of carbon monoxide with chlorine in an exothermic reaction. The reaction occurs at temperatures up to 400°C and in the presence of activated carbon/charcoal as the catalyst to produce Phosgene.
Phosgene is a very hazardous gas, also known scientifically as carbonyl chloride. Long-term phosgene exposure can cause chronic lung damage and other health concerns. To reduce the risk of exposure, it is normally handled by qualified personnel in controlled surroundings, and safety precautions like respiratory protection, ventilation systems, and personal protective equipment are utilized. Phosgene is colorless at room temperature and has a pungent odor comparable to newly cut hay or grass. The chemical formula for Phosgene is COCl2. The molecular weight of Phosgene is 98.92 g/mol, with a boiling temperature of -23.3 °C (-9.94 °F) and a melting point of -130.8 °C (-203.4 °F). It has a density of 4.53 g/L at 25 °C and 1 atm pressure and is mildly soluble in water but soluble in organic solvents such as chloroform, benzene, and ether.
Phosgene Production Cost Processes with Cost Analysis
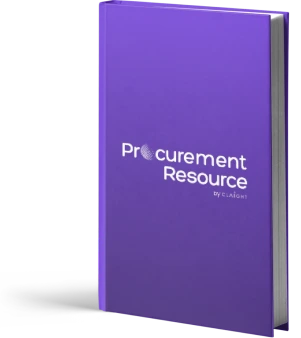
Phosgene Production from Chlorine
The report is a detailed study of economics of production of phosgene from chlorine and its reaction with carbon monoxide in the presence of activated carbon/charcoal as the catalyst at temperatures up to 400°C, in an exothermic reaction to produce Phosgene.
Details: Germany - based plant Q1 2025 From $ 2499.00 USD
Product Details
Particulars | Details |
---|---|
Product Name | Phosgene |
Scope | Manufacturing Process: Process Flow, Material Flow, Material Balance Raw Material and Product Specifications: Raw Material Consumption, Product and Co-product Generation Land and Site Cost: Offsites/Civil Works, Equipment Cost, Auxiliary Equipment Costs, Contingency, Engineering and Consulting Charges, Working Capital Variable Cost: Raw Material, Utilities, Other Variable Costs Fixed Cost: Labor Requirements and Wages, Overhead Expenses, Maintenance Charges, Other Fixed Costs Financing Costs: Interest on Working Capital, Interest on Loans Other Costs: Depreciation Charges, General Sales and Admin Cost |
Currency | US$ (Data can also be provided in the local currency) |
Pricing and Purchase Options | Basic: US$ 2499 Premium: US$ 3499 Enterprise: US$ 4799 |
Customization Scope | The report can be customized as per the requirement of the customer |
Post-Sale Analysts Report | 10-12 weeks of post-purchase analyst support after report delivery for any queries from the deliverable |
Delivery Format | PDF and Excel format through email (editable version in PPT/Word format of the report can be also provided on special request) |
How does our Phosgene Production Cost Report Provide Exhaustive Data and Extensive Insights?
At Procurement Resource, we not only focus on optimizing the should cost of production for Phosgene but also provide our clients with extensive intel and rigorous information on every aspect of the production process. By utilizing a comprehensive cost model, we help you break down expenses related to raw materials, labor, and technology, offering clear pathways to savings. We also assist in evaluating the capital expenditure (CAPEX) and operating expenses (OPEX), which are often measured as cost per unit of production, such as USD/MT, ensuring that your financial planning is aligned with industry benchmarks.
We offer valuable insights on the top technology providers, in-depth supplier database, and best manufacturers, helping you make informed decisions to improve efficiency. Additionally, we design the most feasible layout for your production needs, ensuring the entire process runs smoothly. By minimizing the cash cost of production, we ensure that you stay competitive while securing long-term profitability in the growing Phosgene market. Partnering with Procurement Resource guarantees that every aspect of your production is cost-efficient, advanced, and tailored to your specific requirements.
Key Questions Answered in This Report
- What are the key requirements for setting up a Phosgene manufacturing plant?
- How is Phosgene manufactured?
- What is the process flow involved in producing Phosgene?
- What are the raw material requirements and costs for producing Phosgene?
- What is the total size of land required for setting up a Phosgene manufacturing plant?
- What are the construction requirements for setting up a Phosgene manufacturing plant?
- What are the machinery requirements for producing Phosgene?
- What are the utility requirements and costs for producing Phosgene?
- What are the manpower requirements for producing Phosgene?
- What are the average salaries/wages of manpower working in a Phosgene manufacturing plant?
- What are the packaging requirements and associated costs for Phosgene?
- What are the transportation requirements and associated costs for Phosgene?
- What are the capital costs for setting up a Phosgene manufacturing plant?
- What are the operating costs for setting up a Phosgene manufacturing plant?
- What should be the price of Phosgene?
- What will be the income and expenditures for a Phosgene manufacturing plant?
Need more help?
- We can tailor the report as per your unique requirements such as desired capacity, future expansion plans, product specifications, mode of financing, plant location, etc.
- We can also provide a flexible, easy-to-use, dynamic excel-based cost-model/ dashboard where you can change the inputs to get different outputs
- Speak to our highly skilled team of analysts for insights on the recent trends and innovations, industry best practices, key success and risk factors, product pricing, margins, return on investment, industry standards and regulations, etc.
- Gain an unparalleled competitive advantage in your domain by understanding how to optimize your business operations and maximize profits
- For further assistance, please connect with our analysts
Compare & Choose the Right Report Version for You

You can easily get a quote for any Procurement Resource report. Just click here and raise a request. We will get back to you within 24 hours. Alternatively, you can also drop us an email at sales@procurementresource.com.
RIGHT PEOPLE
At Procurement Resource our analysts are selected after they are assessed thoroughly on having required qualities so that they can work effectively and productively and are able to execute projects based on the expectations shared by our clients. Our team is hence, technically exceptional, strategic, pragmatic, well experienced and competent.
RIGHT METHODOLOGY
We understand the cruciality of high-quality assessments that are important for our clients to take timely decisions and plan strategically. We have been continuously upgrading our tools and resources over the past years to become useful partners for our clientele. Our research methods are supported by most recent technology, our trusted and verified databases that are modified as per the needs help us serve our clients effectively every time and puts them ahead of their competitors.
RIGHT PRICE
Our team provides a detailed, high quality and deeply researched evaluations in competitive prices, that are unmatchable, and demonstrates our understanding of our client’s resource composition. These reports support our clientele make important procurement and supply chains choices that further helps them to place themselves ahead of their counterparts. We also offer attractive discounts or rebates on our forth coming reports.
RIGHT SUPPORT
Our vision is to enable our clients with superior quality market assessment and actionable evaluations to assist them with taking timely and right decisions. We are always ready to deliver our clients with maximum results by delivering them with customised suggestions to meet their exact needs within the specified timeline and help them understand the market dynamics in a better way.
SELECT YOUR LICENCE TYPE
- Review the available license options and choose the one that best fits your needs. Different licenses offer varying levels of access and usage rights, so make sure to pick the one that aligns with your requirements.
- If you're unsure which license is right for you, feel free to contact us for assistance.
CLICK 'BUY NOW'
- Once you've selected your desired report and license, click the ‘Buy Now’ button. This will add the report to your cart. You will be directed to the registration page where you’ll provide the necessary information to complete the purchase.
- You’ll have the chance to review your order and make adjustments, including updating your license or quantity, before proceeding to the next step.
COMPLETE REGISTRATION
- Enter your details for registration. This will include your name, email address, and any other necessary information. Creating an account allows you to easily manage your orders and gain access to future purchases or reports.
- If you already have an account with us, simply log in to streamline the process.
CHOOSE YOUR PAYMENT METHOD
- Select from a variety of secure payment options, including credit/debit cards, PayPal, or other available gateways. We ensure that all transactions are encrypted and processed securely.
- After selecting your payment method, you will be redirected to a secure checkout page to complete your transaction.
CONFIRM YOUR PURCHASE
- Once your payment is processed, you will receive an order confirmation email from sales@procurementresource.com confirming the dedicated project manger and delivery timelines.
ACCESS YOUR REPORT
- The report will be delivered to you by the project manager within the specified timeline.
- If you encounter any issues accessing your report, project manager would remain connected throughout the length of the project. The team shall assist you with post purchase analyst support for any queries or concerns from the deliverable (within the remit of the agreed scope of work).