Cassava Starch Production Cost Reports
Food and Beverages
The report provides a detailed analysis essential for establishing a cassava starch manufacturing plant. It encompasses all critical aspects necessary for cassava starch production, including the cost of cassava starch production, cassava starch plant cost, cassava starch production costs, and the overall cassava starch manufacturing plant cost. Additionally, the study covers specific expenditures associated with setting up and operating a cassava starch production plant. These encompass manufacturing processes, raw material requirements, utility requirements, infrastructure needs, machinery and technology requirements, manpower requirements, packaging requirements, transportation requirements, and more.
Cassava is a complex carbohydrate compound obtained by processing the roots of the cassava plant. It is an organic substance primarily used as a binding component in various products, including paper, cosmetics, and chemical varieties. Cassava Starch is largely used in the food industry, where it is included as an ingredient in bakery products and as a thickening agent to make soups, ice creams, yogurt, noodles, and soft drinks. Similarly, in the paper industry, it is used to improve pulp utilization and quality. Hence, it is used in the production of various paper products, including corrugated cardboard boxes, paper bags, and more.
It is used in textiles to carry out sizing, finishing, and printing owing to its properties like flexibility, abrasion resistance, and for forming a bond with the fiber. Moreover, Cassava Starch is used as a thickening and binding agent in various personal care products, including fragranced balms, body powder, aftershave, and more.
The demand for Cassava Starch is mainly dependent upon its usage in different sectors, including paper, cosmetics, food, and chemical industries. The demand for ready-to-eat (RTE) food products which is rapidly advancing, is boosting the product's demand. Similarly, its usage in the preparation and formulation of cosmetics and paper products (including corrugated cardboard and bags, etc.) fuels its demand in the paper and cosmetics industries.
Industrial Cassava Starch procurement is determined by several factors that are majorly related to its complex market dynamics. Factors including the availability of its raw material (specifically cassava plant for its root that generates Cassava Starch), along with its supply and prices play a vital role and govern its procurement. Similarly, its demand as a binding agent in the paper, cosmetics, and food industries adds up to the factors that influence its procurement on a large scale. Hence, variation in its demand as a thickener in paper, food, and cosmetics significantly impacts its procurement in various regions.
Raw Material for Cassava Starch Production
According to the cassava manufacturing plant project report, the key raw material for Cassava Starch production includes cassava roots (from cassava plant).
Manufacturing Process of Cassava Starch
The extensive Cassava Starch production cost report consists of the major industrial manufacturing process(es):
- From Cassava Roots: Production process of Cassava Starch begins by processing cassava roots. Initially, cassava roots are obtained from cassava plant. The roots are then peeled, washed, and grated. The grated roots are then soaked in water to obtain starch milk, which is then dried to obtain Cassava Starch as the final product.
Cassava Starch is a beady starch derived from the tuberous cassava root's (Manihot esculenta) leaching and drying, which is the source of tapioca and a staple food in the tropics. The plant's roots are leached, dried and ground. After being heated along with the water, it forms a stringy solution which turns thinner with the heating time and thickens when cooled, forming a translucent gel.
The Cassava Starch granules are round in shape with a well-defined hilum and truncated end. The size of the granule is between 5 and 35 μm and has an A-type X-ray diffraction pattern. The starch's nonglucosidic fraction is very low, with the content of protein and lipids below 0.2%. It is comprised of 20% amylose. It is a centrally located dark mark (hilum) and reacts with an iodine/potassium iodide solution resulting in a positive purple colour. Its Gelatinization temperature ranges between 49 - 70 °C.
Cassava Starch Production Cost Processes with Cost Analysis
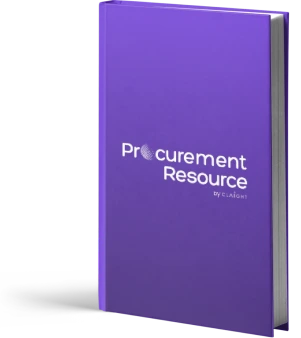
Cassava Starch Production from Wet Milling
This report provides the cost structure of cassava starch production from the wet milling process. In this process, cassava roots are peeled and washed before being grated.
Details: Germany - based plant Q1 2025 From $ 2499.00 USD
Product Details
Particulars | Details |
---|---|
Product Name | Cassava Starch |
Scope | Manufacturing Process: Process Flow, Material Flow, Material Balance Raw Material and Product Specifications: Raw Material Consumption, Product and Co-product Generation Land and Site Cost: Offsites/Civil Works, Equipment Cost, Auxiliary Equipment Costs, Contingency, Engineering and Consulting Charges, Working Capital Variable Cost: Raw Material, Utilities, Other Variable Costs Fixed Cost: Labor Requirements and Wages, Overhead Expenses, Maintenance Charges, Other Fixed Costs Financing Costs: Interest on Working Capital, Interest on Loans Other Costs: Depreciation Charges, General Sales and Admin Cost |
Currency | US$ (Data can also be provided in the local currency) |
Pricing and Purchase Options | Basic: US$ 2499 Premium: US$ 3499 Enterprise: US$ 4799 |
Customization Scope | The report can be customized as per the requirement of the customer |
Post-Sale Analysts Report | 10-12 weeks of post-purchase analyst support after report delivery for any queries from the deliverable |
Delivery Format | PDF and Excel format through email (editable version in PPT/Word format of the report can be also provided on special request) |
How does our Cassava Starch Production Cost Report Provide Exhaustive Data and Extensive Insights?
At Procurement Resource, we not only focus on optimizing the should cost of production for Cassava Starch but also provide our clients with extensive intel and rigorous information on every aspect of the production process. By utilizing a comprehensive cost model, we help you break down expenses related to raw materials, labor, and technology, offering clear pathways to savings. We also assist in evaluating the capital expenditure (CAPEX) and operating expenses (OPEX), which are often measured as cost per unit of production, such as USD/MT, ensuring that your financial planning is aligned with industry benchmarks.
We offer valuable insights on the top technology providers, in-depth supplier database, and best manufacturers, helping you make informed decisions to improve efficiency. Additionally, we design the most feasible layout for your production needs, ensuring the entire process runs smoothly. By minimizing the cash cost of production, we ensure that you stay competitive while securing long-term profitability in the growing Cassava Starch market. Partnering with Procurement Resource guarantees that every aspect of your production is cost-efficient, advanced, and tailored to your specific requirements.
Key Questions Answered in This Report
- What are the key requirements for setting up a Cassava Starch manufacturing plant?
- How is Cassava Starch manufactured?
- What is the process flow involved in producing Cassava Starch?
- What are the raw material requirements and costs for producing Cassava Starch?
- What is the total size of land required for setting up a Cassava Starch manufacturing plant?
- What are the construction requirements for setting up a Cassava Starch manufacturing plant?
- What are the machinery requirements for producing Cassava Starch?
- What are the utility requirements and costs for producing Cassava Starch?
- What are the manpower requirements for producing Cassava Starch?
- What are the average salaries/wages of manpower working in a Cassava Starch manufacturing plant?
- What are the packaging requirements and associated costs for Cassava Starch?
- What are the transportation requirements and associated costs for Cassava Starch?
- What are the capital costs for setting up a Cassava Starch manufacturing plant?
- What are the operating costs for setting up a Cassava Starch manufacturing plant?
- What should be the price of Cassava Starch?
- What will be the income and expenditures for a Cassava Starch manufacturing plant?
Need more help?
- We can tailor the report as per your unique requirements such as desired capacity, future expansion plans, product specifications, mode of financing, plant location, etc.
- We can also provide a flexible, easy-to-use, dynamic excel-based cost-model/ dashboard where you can change the inputs to get different outputs
- Speak to our highly skilled team of analysts for insights on the recent trends and innovations, industry best practices, key success and risk factors, product pricing, margins, return on investment, industry standards and regulations, etc.
- Gain an unparalleled competitive advantage in your domain by understanding how to optimize your business operations and maximize profits
- For further assistance, please connect with our analysts
Compare & Choose the Right Report Version for You

You can easily get a quote for any Procurement Resource report. Just click here and raise a request. We will get back to you within 24 hours. Alternatively, you can also drop us an email at sales@procurementresource.com.
RIGHT PEOPLE
At Procurement Resource our analysts are selected after they are assessed thoroughly on having required qualities so that they can work effectively and productively and are able to execute projects based on the expectations shared by our clients. Our team is hence, technically exceptional, strategic, pragmatic, well experienced and competent.
RIGHT METHODOLOGY
We understand the cruciality of high-quality assessments that are important for our clients to take timely decisions and plan strategically. We have been continuously upgrading our tools and resources over the past years to become useful partners for our clientele. Our research methods are supported by most recent technology, our trusted and verified databases that are modified as per the needs help us serve our clients effectively every time and puts them ahead of their competitors.
RIGHT PRICE
Our team provides a detailed, high quality and deeply researched evaluations in competitive prices, that are unmatchable, and demonstrates our understanding of our client’s resource composition. These reports support our clientele make important procurement and supply chains choices that further helps them to place themselves ahead of their counterparts. We also offer attractive discounts or rebates on our forth coming reports.
RIGHT SUPPORT
Our vision is to enable our clients with superior quality market assessment and actionable evaluations to assist them with taking timely and right decisions. We are always ready to deliver our clients with maximum results by delivering them with customised suggestions to meet their exact needs within the specified timeline and help them understand the market dynamics in a better way.
SELECT YOUR LICENCE TYPE
- Review the available license options and choose the one that best fits your needs. Different licenses offer varying levels of access and usage rights, so make sure to pick the one that aligns with your requirements.
- If you're unsure which license is right for you, feel free to contact us for assistance.
CLICK 'BUY NOW'
- Once you've selected your desired report and license, click the ‘Buy Now’ button. This will add the report to your cart. You will be directed to the registration page where you’ll provide the necessary information to complete the purchase.
- You’ll have the chance to review your order and make adjustments, including updating your license or quantity, before proceeding to the next step.
COMPLETE REGISTRATION
- Enter your details for registration. This will include your name, email address, and any other necessary information. Creating an account allows you to easily manage your orders and gain access to future purchases or reports.
- If you already have an account with us, simply log in to streamline the process.
CHOOSE YOUR PAYMENT METHOD
- Select from a variety of secure payment options, including credit/debit cards, PayPal, or other available gateways. We ensure that all transactions are encrypted and processed securely.
- After selecting your payment method, you will be redirected to a secure checkout page to complete your transaction.
CONFIRM YOUR PURCHASE
- Once your payment is processed, you will receive an order confirmation email from sales@procurementresource.com confirming the dedicated project manger and delivery timelines.
ACCESS YOUR REPORT
- The report will be delivered to you by the project manager within the specified timeline.
- If you encounter any issues accessing your report, project manager would remain connected throughout the length of the project. The team shall assist you with post purchase analyst support for any queries or concerns from the deliverable (within the remit of the agreed scope of work).