Sodium Alginate Production Cost Reports
Food and Beverages
The report provides a detailed analysis essential for establishing a sodium alginate manufacturing plant. It encompasses all critical aspects necessary for sodium alginate production, including the cost of sodium alginate production, sodium alginate plant cost, sodium alginate production costs, and the overall sodium alginate manufacturing plant cost. Additionally, the study covers specific expenditures associated with setting up and operating a sodium alginate production plant. These encompass manufacturing processes, raw material requirements, utility requirements, infrastructure needs, machinery and technology requirements, manpower requirements, packaging requirements, transportation requirements, and more.
Sodium alginate is an organic polysaccharide obtained from brown seaweeds. It is widely utilized as a thickener, emulsifier, and stabilizer in the food, pharmaceutical, textile, and chemical industries. It is widely regarded as safe for human consumption, and regulatory bodies such as the FDA and EFSA have authorized it as a food additive. It can also be used in pharmaceutical and textile sectors for its gelling and binding qualities.
Sodium alginate is also used to make dental impressions and as a medication delivery bioadhesive. It is a non-toxic, food-grade thickener that can be used that can also be included in the formulations of dyes and paints. The compound can be used to produce printing inks that are further used for screen printing, etc.
The market for sodium alginate is strongly driven by its demand observed in the food, pharmaceutical, textile, and chemical industries. Its applications as a food-grade thickener and emulsifier for its gelling and binding ability in food products drive its demand in the food industry. Similarly, its usage for medical and pharmaceutical applications, including the production of bioadhesives to make dental impressions, fuels its demand in the pharmaceutical and healthcare industry. Moreover, its applications in the production of coatings, dyes, and inks for printing increase its demand on a large scale.
There are various factors that impact the procurement of sodium alginate in the global market. Factors including its demand in the food, medical, pharmaceutical, and chemical industries, along with its market prices, production cost, and supply, strongly impact the industrial sodium alginate procurement. The changes in its demand as an emulsifier, thickener, and binding agent in bioadhesives, food products, and coatings, along with the fluctuations observed in its market prices and distribution across various regions, directly influence its procurement around the world.
Raw Material for Sodium Alginate Production
According to the sodium alginate manufacturing plant project report, the key raw material for sodium alginate production includes sodium carbonate.
Manufacturing Process of Sodium Alginate
The extensive sodium alginate production cost report consists of the following major industrial manufacturing process:
- From Seaweed: The production process of sodium alginate is carried out by extraction from seaweed, specifically brown seaweeds (Phaeophyceae). The seaweed is treated in an alkaline solution using sodium carbonate. The alginic acid obtained from the weeds is then collected as precipitates and ion-exchanged to obtain sodium alginate at the end.
Sodium alginate is an organic polysaccharide with a chemical formula of (C6H7NaO6)n. The viscosity of sodium alginate solutions varies according to concentration, temperature, and pH. The viscosity of sodium alginate solutions can range from a few hundred to several thousand centipoises. It dries to produce a thin film, making it ideal as a coating material for a variety of purposes. It can be combined with a variety of components, including other polysaccharides, proteins, and synthetic polymers. It is stable throughout a wide temperature and pH range, making it suitable for a variety of applications that demand stable materials.
Sodium Alginate Production Cost Processes with Cost Analysis
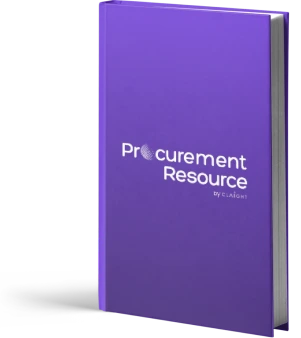
Sodium Alginate Production from Calcium Alginate Method
This report shows the cost structure of sodium alginate production from the calcium alginate method. Wet chopped brown algae are treated with dilute formalin and sodium carbonate solution to form sodium alginate solution.
Details: Germany - based plant Q1 2025 From $ 2499.00 USD
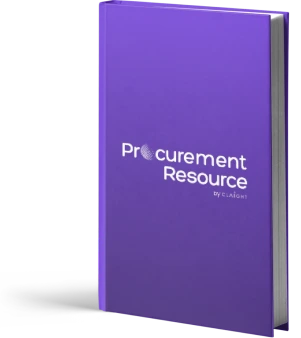
Sodium Alginate Production from Brown Seaweed
This study analyzes Sodium Alginate Production from Brown Seaweed, covering manufacturing, process flow, operating expenses, and financial considerations.
Details: Germany - based plant Q1 2025 From $ 2499.00 USD
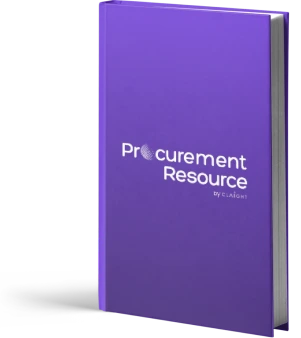
Sodium Alginate Production from Alginic Acid Method
This report provides the cost structure of sodium alginate production from alginic acid. In this process, wet seaweed is chopped and treated with dilute formalin to form sodium alginate solution.
Details: Germany - based plant Q1 2025 From $ 2499.00 USD
Product Details
Particulars | Details |
---|---|
Product Name | Sodium Alginate |
Scope | Manufacturing Process: Process Flow, Material Flow, Material Balance Raw Material and Product Specifications: Raw Material Consumption, Product and Co-product Generation Land and Site Cost: Offsites/Civil Works, Equipment Cost, Auxiliary Equipment Costs, Contingency, Engineering and Consulting Charges, Working Capital Variable Cost: Raw Material, Utilities, Other Variable Costs Fixed Cost: Labor Requirements and Wages, Overhead Expenses, Maintenance Charges, Other Fixed Costs Financing Costs: Interest on Working Capital, Interest on Loans Other Costs: Depreciation Charges, General Sales and Admin Cost |
Currency | US$ (Data can also be provided in the local currency) |
Pricing and Purchase Options | Basic: US$ 2499 Premium: US$ 3499 Enterprise: US$ 4799 |
Customization Scope | The report can be customized as per the requirement of the customer |
Post-Sale Analysts Report | 10-12 weeks of post-purchase analyst support after report delivery for any queries from the deliverable |
Delivery Format | PDF and Excel format through email (editable version in PPT/Word format of the report can be also provided on special request) |
How does our Sodium Alginate Production Cost Report Provide Exhaustive Data and Extensive Insights?
At Procurement Resource, we not only focus on optimizing the should cost of production for Sodium Alginate but also provide our clients with extensive intel and rigorous information on every aspect of the production process. By utilizing a comprehensive cost model, we help you break down expenses related to raw materials, labor, and technology, offering clear pathways to savings. We also assist in evaluating the capital expenditure (CAPEX) and operating expenses (OPEX), which are often measured as cost per unit of production, such as USD/MT, ensuring that your financial planning is aligned with industry benchmarks.
We offer valuable insights on the top technology providers, in-depth supplier database, and best manufacturers, helping you make informed decisions to improve efficiency. Additionally, we design the most feasible layout for your production needs, ensuring the entire process runs smoothly. By minimizing the cash cost of production, we ensure that you stay competitive while securing long-term profitability in the growing Sodium Alginate market. Partnering with Procurement Resource guarantees that every aspect of your production is cost-efficient, advanced, and tailored to your specific requirements.
Key Questions Answered in This Report
- What are the key requirements for setting up a sodium alginate manufacturing plant?
- How is sodium alginate manufactured?
- What is the process flow involved in producing sodium alginate?
- What are the raw material requirements and costs for producing sodium alginate?
- What is the total size of land required for setting up the sodium alginate manufacturing plant?
- What are the construction requirements for setting up a sodium alginate manufacturing plant?
- What are the machinery requirements for producing sodium alginate?
- What are the utility requirements and costs for producing sodium alginate?
- What are the manpower requirements for producing sodium alginate?
- What are the average salaries/wages of manpower working in the sodium alginate manufacturing plant?
- What are the packaging requirements and associated costs for sodium alginate?
- What are the transportation requirements and associated costs for sodium alginate?
- What are the capital costs for setting up the sodium alginate manufacturing plant?
- What are the operating costs for setting up the sodium alginate manufacturing plant?
- What should be the price of precipitated silica?
- What will be the income and expenditures for the sodium alginate manufacturing plant?
Need more help?
- We can tailor the report as per your unique requirements such as desired capacity, future expansion plans, product specifications, mode of financing, plant location, etc.
- We can also provide a flexible, easy-to-use, dynamic excel-based cost-model/ dashboard where you can change the inputs to get different outputs
- Speak to our highly skilled team of analysts for insights on the recent trends and innovations, industry best practices, key success and risk factors, product pricing, margins, return on investment, industry standards and regulations, etc.
- Gain an unparalleled competitive advantage in your domain by understanding how to optimize your business operations and maximize profits
- For further assistance, please connect with our analysts
Compare & Choose the Right Report Version for You

You can easily get a quote for any Procurement Resource report. Just click here and raise a request. We will get back to you within 24 hours. Alternatively, you can also drop us an email at sales@procurementresource.com.
RIGHT PEOPLE
At Procurement Resource our analysts are selected after they are assessed thoroughly on having required qualities so that they can work effectively and productively and are able to execute projects based on the expectations shared by our clients. Our team is hence, technically exceptional, strategic, pragmatic, well experienced and competent.
RIGHT METHODOLOGY
We understand the cruciality of high-quality assessments that are important for our clients to take timely decisions and plan strategically. We have been continuously upgrading our tools and resources over the past years to become useful partners for our clientele. Our research methods are supported by most recent technology, our trusted and verified databases that are modified as per the needs help us serve our clients effectively every time and puts them ahead of their competitors.
RIGHT PRICE
Our team provides a detailed, high quality and deeply researched evaluations in competitive prices, that are unmatchable, and demonstrates our understanding of our client’s resource composition. These reports support our clientele make important procurement and supply chains choices that further helps them to place themselves ahead of their counterparts. We also offer attractive discounts or rebates on our forth coming reports.
RIGHT SUPPORT
Our vision is to enable our clients with superior quality market assessment and actionable evaluations to assist them with taking timely and right decisions. We are always ready to deliver our clients with maximum results by delivering them with customised suggestions to meet their exact needs within the specified timeline and help them understand the market dynamics in a better way.
SELECT YOUR LICENCE TYPE
- Review the available license options and choose the one that best fits your needs. Different licenses offer varying levels of access and usage rights, so make sure to pick the one that aligns with your requirements.
- If you're unsure which license is right for you, feel free to contact us for assistance.
CLICK 'BUY NOW'
- Once you've selected your desired report and license, click the ‘Buy Now’ button. This will add the report to your cart. You will be directed to the registration page where you’ll provide the necessary information to complete the purchase.
- You’ll have the chance to review your order and make adjustments, including updating your license or quantity, before proceeding to the next step.
COMPLETE REGISTRATION
- Enter your details for registration. This will include your name, email address, and any other necessary information. Creating an account allows you to easily manage your orders and gain access to future purchases or reports.
- If you already have an account with us, simply log in to streamline the process.
CHOOSE YOUR PAYMENT METHOD
- Select from a variety of secure payment options, including credit/debit cards, PayPal, or other available gateways. We ensure that all transactions are encrypted and processed securely.
- After selecting your payment method, you will be redirected to a secure checkout page to complete your transaction.
CONFIRM YOUR PURCHASE
- Once your payment is processed, you will receive an order confirmation email from sales@procurementresource.com confirming the dedicated project manger and delivery timelines.
ACCESS YOUR REPORT
- The report will be delivered to you by the project manager within the specified timeline.
- If you encounter any issues accessing your report, project manager would remain connected throughout the length of the project. The team shall assist you with post purchase analyst support for any queries or concerns from the deliverable (within the remit of the agreed scope of work).