Potassium Alginate Manufacturing Plant Project Report: Key Insights and Outline
Potassium Alginate Manufacturing Plant Project Report by Procurement Resource thoroughly focuses on every detail that encompasses the cost of manufacturing. Our extensive cost model meticulously covers breaking down Potassium Alginate plant capital cost around raw materials, labour, technology, and manufacturing expenses. This enables precise cost structure optimization and helps in identifying effective strategies to reduce the overall Potassium Alginate manufacturing plant cost and the cash cost of manufacturing.
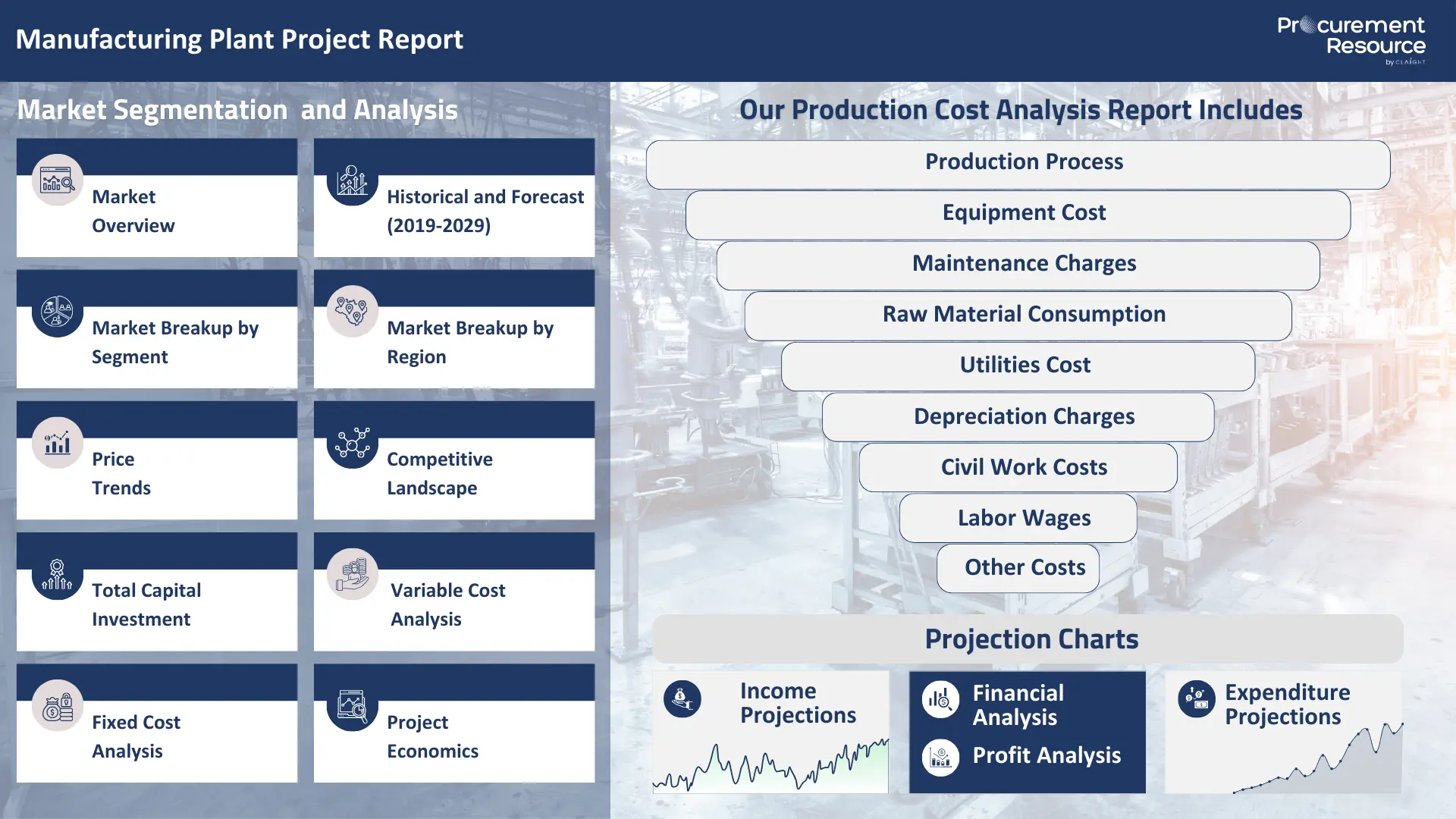
Planning to Set Up a Potassium Alginate Plant? Request a Free Sample Project Report Now!
Potassium alginate is a naturally derived polysaccharide which is extracted from brown seaweed. It is highly valued for its excellent gelling, thickening, stabilising, and emulsifying properties. It appears as a white to yellowish-brown fibrous powder or granules. It serves as a versatile hydrocolloid, and it also finds its use as a food additive in the food and beverage industry. It is also used as a crucial component in pharmaceuticals, cosmetics, and various industrial applications.
Applications of Potassium Alginate
Potassium alginate finds various essential industrial applications due to its remarkable hydrocolloid properties as a gelling agent, thickener, stabiliser, and emulsifier. It is widely used across several industrial sectors, which are given below:
- Food and Beverage Industry (Major Application): Potassium alginate finds significant applications in the food industry.
- Thickener and Stabiliser: It is used in dairy products like ice cream, yoghurt, cheese, as well as sauces, dressings, and gravies to improve texture, prevent syneresis (water separation), and enhance stability.
- Gelling Agent: It helps in creating heat-stable gels in desserts, jellies, fruit preparations, and structured foods, such as structured meat products and vegetarian analogues.
- Emulsifier: It stabilises emulsions in various food systems, such as margarine and processed cheese.
- Encapsulation: It is also used for encapsulating flavours, vitamins, and active ingredients due to its gentle gelling properties.
- Bakery Products: It also helps in improving dough elasticity and moisture retention in bread and pastries.
- Pharmaceuticals (Significant Application): Potassium alginate is widely used in various pharmaceutical formulations.
- Binding Agent: It is used as a binder in tablet formulations, which helps to hold ingredients together.
- Disintegrant: It also works as a disintegrant, which helps tablets break apart rapidly in the digestive tract.
- Controlled Release: It is also used in sustained-release drug delivery systems due to its gelling capabilities, which allow for slow drug release.
- Antacids: It also forms a raft in the stomach to prevent reflux in certain antacid preparations.
- Cosmetics and Personal Care Products:
- Thickener and Stabiliser: It is often used as an ingredient in lotions, creams, shampoos, and toothpastes to provide desired stability.
- Film-Former: It forms protective films on skin or hair.
- Medical and Dental Applications (Niche):
- Wound Dressings: It is also used in highly absorbent wound dressings due to its ability to form a gel in contact with exudates to promote healing.
- Dental Impressions: It is also used as a gelling agent in dental impression materials.
- Textile Printing: It also finds its application as a thickening agent in textile printing pastes to achieve sharp prints.
Top 5 Industrial Manufacturers of Potassium Alginate
The potassium alginate manufacturing includes companies specialising in hydrocolloids and seaweed-derived products. The following are the key manufacturers:
- DuPont Nutrition & Biosciences (now IFF - International Flavours & Fragrances): A major global player in food ingredients and hydrocolloids. DuPont's legacy in alginates is now part of IFF's extensive portfolio, which makes them a significant manufacturer of potassium alginate and other alginate products.
- Kimica Corporation: A Japanese company, Kimica is one of the world's leading manufacturers of alginates from seaweed. They produce various grades of potassium alginate for food, pharmaceutical, and industrial applications.
- Bright Moon Seaweed Group Co., Ltd. (China): A prominent Chinese manufacturer and supplier specialising in seaweed processing and alginates. They are a significant global producer of potassium alginate and other alginate derivatives, serving diverse markets.
- FMC Corporation (now J. RETTENMAIER & SÖHNE GmbH + Co KG - JRS): JRS is a key player in the alginate market, producing and supplying potassium alginate worldwide.
- Shandong Jiejing Group Co., Ltd. (China): Another major Chinese manufacturer involved in seaweed processing and the production of alginates, including potassium alginate, for the international market.
Feedstock for Potassium Alginate and Its Market Dynamics
The main feedstock for potassium alginate production is brown seaweed and caustic soda.
Major Feedstocks and Their Market Dynamics
- Brown Seaweed (e.g., Laminaria, Ascophyllum, Macrocystis):
- Source: Brown seaweed is harvested from coastal waters around the world, particularly in regions like China, Norway, Chile, and France. It is a natural, renewable marine resource.
- Market Dynamics: The price of brown seaweed is influenced by harvesting costs (labour, specialised vessels), weather conditions affecting growth and harvest yields, and environmental regulations on harvesting practices. Sustainable harvesting practices (e.g., replanting, rotational harvesting) are gaining importance but can add to costs. Quality (alginate content, impurity levels) varies by species and harvest location.
- Industrial Procurement: Industrial procurement involves sourcing from specialised seaweed harvesting companies or direct harvesting operations by integrated manufacturers. The seasonality and geographical nature of seaweed supply are important for supply chain optimisation.
- Caustic Soda (Sodium Hydroxide - NaOH):
- Production: Caustic soda is a fundamental inorganic chemical produced primarily through the chlor-alkali process (electrolysis of sodium chloride brine). Chlorine gas and hydrogen gas are co-products.
- Market Dynamics: Its price is highly sensitive to electricity costs (for electrolysis) and the supply-demand balance of chlorine (its co-product).
- Industrial Procurement: Industrial procurement of caustic soda depends on the outcome from large chlor-alkali producers. Its market price fluctuation largely depends on the chlorine market.
Dynamics Affecting Raw Materials
The dynamics affecting these raw materials are crucial for determining the overall manufacturing expenses of potassium alginate.
- Environmental Regulations on Seaweed Harvesting: Increasing environmental awareness and regulations regarding marine ecosystems and sustainable harvesting can impact seaweed availability and increase raw material costs.
- Climate Change Impacts: Ocean temperatures, currents, and acidification can affect seaweed growth rates and abundance, introducing volatility into the feedstock supply.
- Energy Costs for Caustic Soda: As caustic soda production is highly electricity-intensive, fluctuations in electricity prices directly impact its raw material cost, influencing the production cost analysis.
- Purity Requirements: The need for food-grade or pharmaceutical-grade potassium alginate demands careful control of impurities from both seaweed (e.g., heavy metals) and caustic soda, requiring potentially more extensive purification, impacting the overall cost model.
- Transportation Costs: The cost of transporting bulky, often wet, brown seaweed from coastal harvesting sites to processing plants, and caustic soda to the potassium alginate manufacturing plant, adds to the manufacturing expenses.
Market Drivers for Potassium Alginate
The market for potassium alginate is experiencing consistent growth, which is influenced by several key factors that also affect investment cost decisions and the overall return on investment (ROI) projects.
- Growing Demand for Natural and Clean Label Food Ingredients (Primary Driver): The rising consumer preference for natural, non-GMO, and "clean label" food additives drives demand for potassium alginate. Its natural origin from brown seaweed makes it a preferred choice over synthetic stabilisers and thickeners, which further boosts potassium alginate consumption and demand in food and beverages.
- Expansion of Processed Food and Beverage Industry: The continuous growth of the global food processing industry, including dairy, confectionery, sauces, and baked goods, fuels the need for effective gelling agents, thickeners, and stabilisers like potassium alginate. The increasing consumer demand for natural food ingredients, as well as functional benefits in food, pharma, and personal care, significantly ensures consistent and high potassium alginate consumption.
- Increasing Applications in Pharmaceuticals and Nutraceuticals: The expanding pharmaceutical industry and the rising demand for nutraceuticals also drive the use of potassium alginate in tablet binding, controlled drug release, and antacid formulations.
- Growth in Cosmetics and Personal Care: The booming personal care market utilises potassium alginate as a natural thickener, stabiliser, and film-former in various cosmetic products, which also gets promoted with green beauty trends.
- Innovation in Medical Applications: Research and development in advanced wound care dressings and tissue engineering continue to explore the unique gelling and biocompatible properties of alginates, including potassium alginate, for high-value medical applications.
- Geographical Market Dynamics:
- Asia-Pacific (APAC): China is the largest producer and consumer of potassium alginate, due to its major seaweed resources, a large food processing industry, and competitive manufacturing expenses. Countries like China and South Korea are major producers and exporters of potassium Alginate.
- Europe: Maintains a significant market share due to its well-established food industry and strong emphasis on natural food ingredients. Countries like Norway and France have notable seaweed resources and processing capabilities.
- North America: This region shows consistent demand, which is driven by a mature food and pharmaceutical industry and increasing consumer interest in natural food additives.
All these market drivers ensure a strong and expanding market outlook for potassium alginate, which encourages cost structure optimisation for producers.
Capital and Operational Expenses for a Potassium Alginate Plant
Establishing a potassium alginate manufacturing plant involves a combined cost structure of Potassium Alginate Plant capital cost and operating expenses (OPEX). A detailed cost model and production cost analysis are essential for determining economic feasibility and optimisation of the overall potassium alginate plant cost.
Capital Expenditure (CAPEX): Potassium Alginate Plant Capital Cost
The total capital expenditure (CAPEX) for a potassium alginate plant covers all upfront costs required for seaweed processing, extraction, chemical conversion, purification, and drying. Given below are the major components of the overall investment cost.
- Site Acquisition and Preparation (5-8% of Total CAPEX):
- Land Acquisition: Purchasing suitable industrial land, ideally near coastal areas, for direct access to brown seaweed feedstock.
- Site Development: Foundations for large tanks, crushers, filters, and dryers, internal roads, drainage systems, and robust utility connections.
- Seaweed Pre-processing Section (10-15% of Total CAPEX):
- Selection and Drying: Facilities for sorting and natural or artificial drying (e.g., rotary dryers, belt dryers) of brown seaweed after harvesting.
- Crushing/Grinding Equipment: Heavy-duty crushers, shredders, or hammer mills for reducing the dried seaweed into a fine powder or small pieces to facilitate extraction.
- Storage: Silos for dried, crushed seaweed.
- Extraction and Acid Treatment Section (15-25% of Total CAPEX):
- Reaction/Extraction Tanks: These are the large agitated tanks where crushed seaweed is treated with acidic water (e.g., sulfuric acid, hydrochloric acid). These tanks must be corrosion-resistant.
- Washing Systems: For washing the seaweed residue to remove impurities and prepare for alginic acid extraction.
- Filtration/Separation Units: For separating the initial insoluble seaweed residue from the crude alginic acid solution. This may involve filter presses, centrifuges, or decanters.
- Alginic Acid Conversion and Precipitation Section (20-30% of Total CAPEX):
- Neutralisation Tanks: Where the alginic acid (initially insoluble) is treated with caustic soda (sodium hydroxide) to convert it into water-soluble sodium alginate. Requires efficient mixing and temperature control.
- Sodium Alginate Filtration: Further filtration to clarify the water-soluble sodium alginate solution from any remaining insoluble impurities.
- Acid Precipitation Reactor: A reactor where an acid (e.g., sulfuric acid, hydrochloric acid) is added to the sodium alginate solution to precipitate insoluble alginic acid again. This is a crucial purification step.
- Filtration/Centrifugation: For separating the precipitated insoluble alginic acid cake from the solution
- Ion Exchange Section (10-15% of Total CAPEX):
- Ion Exchange Columns: Columns packed with ion-exchange resins. This is where the purified alginic acid is converted into potassium alginate. The hydrogen ions on the alginic acid are exchanged for potassium ions. The resins themselves are a significant capital cost and require regeneration systems.
- Regeneration System: For regenerating the ion-exchange resin (e.g., using potassium chloride solution).
- Drying and Milling Section (10-15% of Total CAPEX):
- Dryer: For converting the wet potassium alginate (often a gel or granular material) into a dry powder or granular form. This could involve fluid bed dryers, spray dryers, or belt dryers. This is a significant capital cost and energy consumer.
- Milling/Grinding Equipment: Hammer mills, pin mills, or pulverisers for milling the dried potassium alginate to the desired particle size.
- Finished Product Storage and Packaging (5-8% of Total CAPEX):
- Storage Silos/Bins: For storing dried, milled potassium alginate.
- Packaging Equipment: Bagging machines, drum fillers, or specialised packaging for food/pharmaceutical grades, often with moisture-barrier packaging.
- Utility Systems (10-15% of Total CAPEX):
- Steam Generation: Boilers for heating reactors, dryers, and processing.
- Cooling Water System: Cooling towers and pumps.
- Electrical Distribution: Standard industrial electrical systems.
- Compressed Air System: For pneumatic controls.
- Wastewater Treatment Plant: Facilities for treating process wastewater (e.g., acidic/alkaline streams, wash water, spent brine from ion exchange) to meet environmental discharge regulations.
- Automation and Instrumentation (5-10% of Total CAPEX):
- Distributed Control System (DCS) / PLC systems for precise monitoring and control of temperature, pH, flow, and concentration throughout the multi-step process.
- Quality Control Laboratory: Equipped for rigorous in-process testing and final product analysis to ensure compliance with food/pharmaceutical standards.
- Engineering, Procurement, and Construction (EPC) Costs (10-15% of Total CAPEX):
- Includes detailed process design, material sourcing for corrosion resistance, construction of facilities, and rigorous commissioning.
Operating Expenditure (OPEX):
Operating expenses (OPEX) are the ongoing costs required to sustain uninterrupted and efficient production of potassium alginate.
- Raw Material Costs (Approx. 40-60% of Total OPEX):
- Brown Seaweed: The largest single raw material expense. Its cost is heavily influenced by harvest yields, seasonality, and harvesting costs.
- Caustic Soda (Sodium Hydroxide): The Cost of caustic soda, influenced by electricity and chlorine prices.
- Acids (Sulfuric Acid/Hydrochloric Acid): For initial seaweed treatment and precipitation of alginic acid.
- Potassium Source (e.g., Potassium Chloride): For regenerating the ion-exchange resin to introduce potassium ions. This is a significant cost.
- Process Water: Large volumes for extraction, washing, and processing.
- Utility Costs (Approx. 15-25% of Total OPEX):
- Energy: Mainly covers electricity for crushing, pumping, stirring, and running dryers. Heat (steam) for initial drying of seaweed, and heating during extraction/dissolution steps. Drying and evaporation (if done) are also major energy consumers, directly impacting operational cash flow.
- Cooling Water: For process cooling.
- Labour Costs (Approx. 8-15% of Total OPEX):
- Salaries, wages, and benefits for skilled operators, maintenance staff, and QC personnel. Seaweed processing can be labour-intensive.
- Maintenance and Repairs (Approx. 3-6% of Fixed Capital):
- Routine preventative maintenance programs, unscheduled repairs, and replacement of parts for crushers, tanks (acidic conditions), filters, and dryers. This includes lifecycle cost analysis for major equipment.
- Waste Management and Environmental Compliance (2-4% of Total OPEX):
- Costs associated with treating and disposing of process wastewater (e.g., acidic/alkaline streams, spent brine from ion exchange, residual seaweed biomass) to meet environmental discharge regulations.
- Depreciation and Amortisation (Approx. 5-10% of Total OPEX):
- Non-cash expenses that account for the wear and tear of the total capital expenditure (CAPEX) assets over their useful life. These are important for financial reporting and break-even point analysis.
- Indirect Operating Costs (Variable):
- Insurance premiums, property taxes, and expenses for research and development aimed at improving production efficiency metrics or exploring new cost structure optimisation strategies (e.g., new extraction methods, enzyme use).
- Logistics and Distribution: Costs for transporting bulky brown seaweed from coastal areas to the plant, and finished potassium alginate to customers.
Manufacturing Process
This report comprises a thorough value chain evaluation for potassium alginate manufacturing and consists of an in-depth production cost analysis revolving around industrial potassium alginate manufacturing.
Production from Brown Seaweed and Caustic Soda:
- The process involves multiple stages of extraction, chemical conversion, and purification from natural seaweed. Potassium alginate production starts by choosing and drying brown seaweed, which is then crushed to prepare for extraction. The crushed seaweed is treated with acidic water to pull out alginic acid. Next, caustic soda is added to turn the alginic acid into sodium alginate, which dissolves in water. After filtering this solution, an acid is added to make the alginic acid precipitate out as a solid again. Then, an ion exchange process converts this solid into potassium alginate. Finally, the obtained solid is dried and ground to form potassium alginate as the final product, ready for use.
Properties of Potassium Alginate
Potassium alginate is the potassium salt of alginic acid, which is also a linear polysaccharide. Its complex polymeric structure and ability to form viscous solutions and gels are key to its diverse industrial applications.
Physical Properties:
- Appearance: appears as a white to yellowish-brown fibrous powder or granular solid. The colour can vary based on the seaweed source and purification.
- Odour: It is generally odourless, which makes it suitable for food and pharmaceutical applications.
- Molecular formula: (C6H7O6K)n
- Solubility: Highly soluble in cold and hot water, forming viscous, colloidal solutions. It is insoluble in alcohol, ether, and chloroform. This excellent aqueous solubility is crucial for its use as a thickener, stabiliser, and gelling agent.
- Viscosity: Forms highly viscous solutions at relatively low concentrations. The viscosity depends on the molecular weight of the alginate, concentration, temperature, and presence of other ions.
- Gelling Properties: Unlike some other alginates (like calcium alginate), potassium alginate generally forms heat-stable gels when combined with certain polyvalent cations (especially calcium ions). It can also form thermoreversible gels under specific conditions.
- Film-Forming Ability: It can form flexible, clear films upon drying.
- Pseudoplasticity: Its solutions exhibit pseudoplastic (shear-thinning) behaviour, meaning their viscosity decreases under shear stress (e.g., stirring, pumping) and recovers when the stress is removed. This is desirable for ease of processing in food and cosmetic formulations.
Chemical Properties:
- Polysaccharide Structure: Potassium alginate is a linear, unbranched polysaccharide composed of two types of uronic acid units: β-D-mannuronic acid (M) and α-L-guluronic acid (G).
- Ionic Polymer: The carboxylic acid groups on the uronic acid units are deprotonated to form carboxylate anions, which are balanced by potassium cations (K?). This makes it an anionic polysaccharide.
- Ion-Exchange Properties: The carboxylate groups can exchange ions, binding to other metal cations. This property is utilised in its manufacturing (ion exchange step) and for chelating metal ions in various applications.
- Stability: Solutions are generally stable over a wide pH range (e.g., pH 4-10) but can undergo depolymerisation (viscosity loss) at very low pH (highly acidic conditions) or very high temperatures. It also undergoes polymerisation in the presence of metal ions that can catalyse degradation.
- Biodegradability: Potassium alginate is biodegradable, as it is a natural polysaccharide.
- Non-toxic: It is widely regarded as non-toxic and biocompatible, which makes it suitable for food, pharmaceutical, and medical uses.
Potassium Alginate Manufacturing Plant Report provides you with a detailed assessment of capital investment costs (CAPEX) and operational expenses (OPEX), generally measured as cost per metric ton (USD/MT). This approach ensures that your investment decisions are aligned with the latest industry standards and economic feasibility metrics, enhancing your manufacturing efficiency and financial planning.
Apart from that, this Potassium Alginate manufacturing plant report also covers the leading technology providers that help you plan a robust plan of action related to Potassium Alginate manufacturing plant and its production process(es), and also by helping you with an in-depth supplier database. This report provides exclusive insights into the best manufacturing practices for Potassium Alginate and technology implementation costs. This report also covers operational cash flow, fixed and variable costs, and detailed break-even point analysis, ensuring that your manufacturing process is not only efficient but also economically viable in the competitive market landscape.
In addition to operational insights, the Potassium Alginate manufacturing plant report also comprehensively focuses on lifecycle cost analysis, maintenance costs, and energy consumption costs, which are critical for maintaining long-term sustainability and profitability. Our manufacturing cost analysis extends to include regulatory compliance costs, inventory holding costs, and logistics and distribution costs, providing a holistic view of the potential expenses and savings
We at Procurement Resource ensure that this report is not only cost-efficient, environmentally sustainable, and aligned with the latest technological advancements but also that you are equipped with all necessary tools to optimize supply chain operations, manage risks effectively, and achieve superior market positioning for Potassium Alginate.
Key Insights and Report Highlights
Report Features |
Details |
Report Title |
Potassium Alginate Manufacturing Plant Project Report |
Preface |
Overview of the study and its significance. |
Scope and Methodology |
Key Questions Answered, Methodology, Estimations & Assumptions. |
Executive Summary |
Global Market Scenario, Production Cost Summary, Income Projections, Expenditure Projections, Profit Analysis. |
Global Market Insights |
Market Overview, Historical and Forecast (2019-2029), Market Breakup by Segment, Market Breakup by Region, Price Trends (Raw Material Price Trends, Potassium Alginate Price Trends), Competitive Landscape (Key Players, Profiles of Key Players). |
Detailed Process Flow |
Product Overview, Properties and Applications, Manufacturing Process Flow, Process Details. |
Project Details |
Total Capital Investment, Land and Site Cost, Offsites/Civil Works Cost, Plant Machinery Cost, Auxiliary Equipment Cost, Contingency, Consulting and Engineering Charges, Working Capital. |
Variable Cost Analysis |
Raw Material Specifications, Raw Material Consumption, Raw Material Costs, Utilities Consumption and Costs, Co-product Cost Credit, Labour Requirements and Costs. |
Fixed Cost Analysis |
Plant Repair & Maintenance Cost, Overheads Cost, Insurance Cost, Financing Costs, Depreciation Charges. |
General Sales and Administration Costs |
Costs associated with sales and administration |
Project Economics |
Techno-economic Parameters, Income Projections, Expenditure Projections, Financial Analysis (Payback Period, Net Present Value, Internal Rate of Return), Profit Analysis, Production Cost Summary. |
Report Format |
PDF for BASIC and PREMIUM; PDF+Dynamic Excel for ENTERPRISE. |
Pricing and Purchase Options |
BASIC: USD 2999
PREMIUM: USD 3999
ENTERPRISE: USD 5999 |
Customization Scope |
The report can be customized based on the customer’s requirements. |
Post-Sale Analyst Support |
10-12 Weeks of support post-sale. |
Delivery Format |
PDF and Excel via email; editable versions (PPT/Word) on special request. |
Key Questions Covered in our Potassium Alginate Manufacturing Plant Report
- How can the cost of producing Potassium Alginate be minimized, cash costs reduced, and manufacturing expenses managed efficiently to maximize overall efficiency?
- What is the estimated Potassium Alginate manufacturing plant cost?
- What are the initial investment and capital expenditure requirements for setting up a Potassium Alginate manufacturing plant, and how do these investments affect economic feasibility and ROI?
- How do we select and integrate technology providers to optimize the production process of Potassium Alginate, and what are the associated implementation costs?
- How can operational cash flow be managed, and what strategies are recommended to balance fixed and variable costs during the operational phase of Potassium Alginate manufacturing?
- How do market price fluctuations impact the profitability and cost per metric ton (USD/MT) for Potassium Alginate, and what pricing strategy adjustments are necessary?
- What are the lifecycle costs and break-even points for Potassium Alginate manufacturing, and which production efficiency metrics are critical for success?
- What strategies are in place to optimize the supply chain and manage inventory, ensuring regulatory compliance and minimizing energy consumption costs?
- How can labor efficiency be optimized, and what measures are in place to enhance quality control and minimize material waste?
- What are the logistics and distribution costs, what financial and environmental risks are associated with entering new markets, and how can these be mitigated?
- What are the costs and benefits associated with technology upgrades, modernization, and protecting intellectual property in Potassium Alginate manufacturing?
- What types of insurance are required, and what are the comprehensive risk mitigation costs for Potassium Alginate manufacturing?
1 Preface
2 Scope and Methodology
2.1 Key Questions Answered
2.2 Methodology
2.3 Estimations & Assumptions
3 Executive Summary
3.1 Global Market Scenario
3.2 Production Cost Summary
3.3 Income Projections
3.4 Expenditure Projections
3.5 Profit Analysis
4 Global Potassium Alginate Market
4.1 Market Overview
4.2 Historical and Forecast (2019-2029)
4.3 Market Breakup by Segment
4.4 Market Breakup by Region
4.6 Price Trends
4.6.1 Raw Material Price Trends
4.6.2 Potassium Alginate Price Trends
4.7 Competitive Landscape
4.8.1 Key Players
4.8.2 Profiles of Key Players
5 Detailed Process Flow
5.1 Product Overview
5.2 Properties and Applications
5.3 Manufacturing Process Flow
5.4 Process Details
6 Project Details, Requirements and Costs Involved
6.1 Total Capital Investment
6.2 Land and Site Cost
6.3 Offsites/ Civil Works Cost
6.4 Plant Machinery Cost
6.5 Auxiliary Equipment Cost
6.6 Contingency, Consulting and Engineering Charges
6.6 Working Capital
7 Variable Cost Analysis
7.1 Raw Materials
7.1.1 Raw Material Specifications
7.1.2 Raw Material Consumption
7.1.3 Raw Material Costs
7.2 Utilities Consumption and Costs
7.3 Co-product Cost Credit
7.4 Labour Requirements and Costs
8 Fixed Cost Analysis
8.1 Plant Repair & Maintanence Cost
8.2 Overheads Cost
8.3 Insurance Cost
8.4 Financing Costs
8.5 Depreciation Charges
9 General Sales and Administration Costs
10 Project Economics
10.1 Techno-economic Parameters
10.2 Income Projections
10.3 Expenditure Projections
10.4 Financial Analysis
10.5 Profit Analysis
10.5.1 Payback Period
10.5.2 Net Present Value
10.5.3 Internal Rate of Return
11 References