Sulfamic Acid Manufacturing Plant Project Report: Key Insights and Outline
Sulfamic Acid Manufacturing Plant Project Report by Procurement Resource thoroughly focuses on every detail that encompasses the cost of manufacturing. Our extensive cost model meticulously covers breaking down Sulfamic Acid plant capital cost around raw materials, labour, technology, and manufacturing expenses. This enables precise cost structure optimization and helps in identifying effective strategies to reduce the overall Sulfamic Acid manufacturing plant cost and the cash cost of manufacturing.
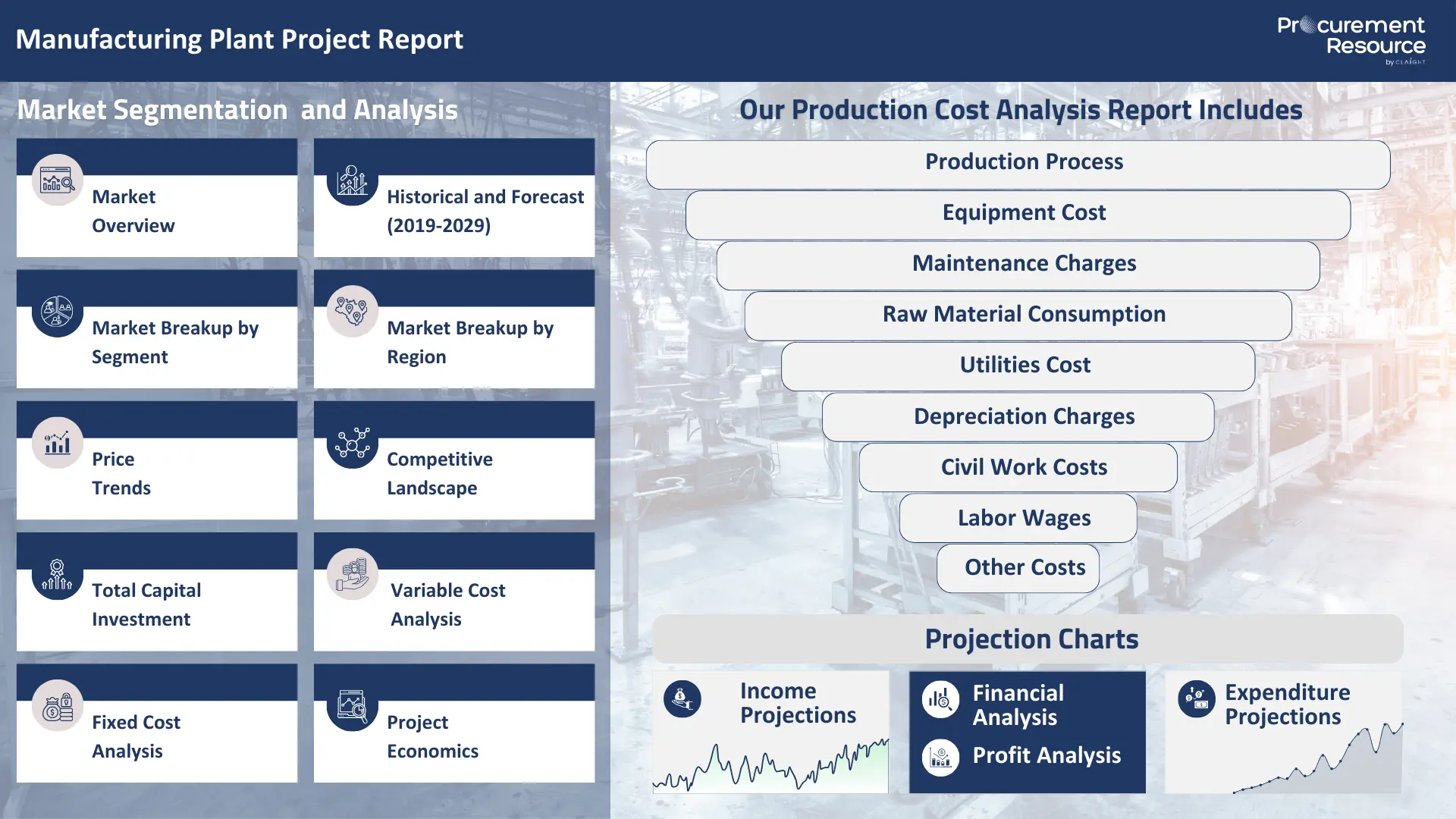
Planning to Set Up a Sulfamic Acid Plant? Request a Free Sample Project Report Now!
Sulfamic Acid is a white, crystalline, odourless inorganic acid known for its strong acidic properties, combined with low corrosiveness, volatility, and toxicity, compared to other chemicals. This unique profile makes it a versatile chemical with several industrial applications.
The top industries where Sulfamic Acid finds significant industrial applications include:
- Industrial Cleaning and Descaling: This is a primary application of Sulfamic Acid. It is widely used as a descaling agent to remove limescale, rust, and mineral deposits from industrial equipment, such as boilers, cooling towers, heat exchangers, condensers, and pipelines. Its low corrosiveness makes it preferable to hydrochloric acid for these purposes. It also finds use in cleaning dairy and brewery equipment to remove milkstone and beerstone.
- Dyes and Sulfamic Acid Industry: Sulfamic Acid is also used in the manufacturing of dyes and pigments. It effectively removes excess nitrites from diazotisation reactions, which ensures colour purity and stability. It is also used as a mordant in the dyeing of leather and textiles.
- Pulp and Paper Industry: In this sector, Sulfamic Acid acts as a chloride stabiliser during the bleaching process of pulp. It inhibits degradation due to temperature at the chlorination stage, facilitating bleaching at elevated temperatures and lower pH, while maintaining pulp strength.
- Pharmaceuticals: Sulfamic Acid also serves as a raw material in the synthesis of various pharmaceutical compounds, including certain antiviral and anticancer medications. It is also used in the preparation of synthetic sweeteners like sodium cyclamate.
- Electroplating and Metal Finishing: It is non-corrosive and can form water-soluble salts with metals. Therefore, it is used in electroplating baths and for metal cleaning and finishing to provide a smoother and more uniform finish.
- Herbicide Manufacturing: Sulfamic acid is often utilised as a starting material for the production of herbicides like ammonium sulfamate.
- Other Applications: The compound also finds applications as a catalyst for esterification processes, a coagulator for urea-formaldehyde resins, and an ingredient in fire extinguishing media.
Top 5 Manufacturers of Sulfamic Acid
The global Sulfamic Acid manufacturing market is served by several key players who fulfil industrial needs. Here are five significant industrial manufacturers:
- Yantai Sanding Chemical Co., Ltd. (China)
- Laizhou Guangcheng Chemical Co. (China): It serves as another key player from China, which contributes significantly to the global supply chain of sulfamic acid.
- Nippon Shokubai Co., Ltd. (Japan): A global chemical company involved in manufacturing various speciality chemicals, including intermediates like sulfamic acid.
- BASF SE (Germany): A leading global chemical company with a broad range of chemicals, including various industrial chemicals like Sulfamic Acid.
- Shree Ram Chemicals (India): An Indian manufacturer with a notable presence in the domestic market, serving the growing industrial procurement needs in India.
Feedstock for Sulfamic Acid Production and Market Dynamics
The industrial manufacturing process of Sulfamic Acid depends on the availability of these industrial chemicals, such as urea, sulfur trioxide, and sulfuric acid. The value chain evaluation and dynamics affecting these feedstock components are crucial for production cost analysis and ensuring cost structure optimisation.
The primary raw materials (feedstock) for the Sulfamic Acid Manufacturing process are:
- Urea (CO(NH2)2): A widely produced nitrogen-containing organic compound.
- Market Dynamics: Urea is primarily used as a fertiliser, so its market is heavily influenced by agricultural demand, natural gas prices (as natural gas is a primary feedstock for ammonia, a precursor to urea), and global trade policies. Fluctuations in these factors directly impact the cost per metric ton (USD/MT) of urea, along with the cash cost of production for sulfamic acid.
- Sulfur Trioxide (SO3): It is produced by the catalytic oxidation of sulfur dioxide (SO2), which is derived from burning elemental sulfur or from metallurgical operations.
- Market Dynamics: The availability and price of sulfur trioxide are closely linked to the global sulfur market and sulfuric acid production. Sulfur prices can fluctuate due to supply from oil and gas desulfurisation (by-product sulfur) and demand from fertiliser production. Environmental regulations on sulfur emissions also influence its recovery and pricing.
- Sulfuric Acid (H2SO4): It is one of the most widely produced industrial chemicals.
- Market Dynamics: Sulfuric acid production is primarily driven by the fertiliser industry (phosphate fertilisers), as well as by metal processing, petroleum refining, and chemical synthesis. Its production cost analysis is heavily influenced by sulfur prices and energy costs for the contact process. Global economic growth and geo-locations with significant mining or chemical industries also impact their availability and pricing. Asia-Pacific, particularly China and India, are major consumption hubs, and local production capabilities, which influence industrial procurement costs.
Therefore, the value chain evaluation for Sulfamic Acid is impacted by global agricultural trends (for urea), energy markets (for sulfur trioxide and sulfuric acid production), and environmental regulations. Any significant market price fluctuation in these raw materials will directly affect the manufacturing expenses and overall economic feasibility of Sulfamic Acid manufacturing.
Market Drivers for Sulfamic Acid
- The market for Sulfamic Acid is driven by demand as a major component across multiple industries, such as textiles, pulp & paper, pharmaceuticals, and industrial cleaning.
- Increasing Industrial Cleaning Demands: The primary driver for Sulfamic Acid is its growing adoption as a safer and more effective alternative to traditional strong mineral acids (like hydrochloric acid) for descaling and industrial cleaning. The need for efficient maintenance of industrial equipment across manufacturing, food processing, and chemical sectors worldwide fuels its demand and drives industrial Sulfamic Acid procurement.
- Growth in Chemical and Pharmaceutical Industries: The expanding chemical synthesis and pharmaceutical sectors, particularly in the Asia-Pacific region, drive the demand for Sulfamic Acid, a key reagent and intermediate. The development of new drug compounds and chemical processes also necessitates a reliable supply of this acid.
- Expansion of the Pulp & Paper Industry: The rising global demand for paper and paper products, particularly in emerging economies, directly translates to increased consumption of Sulfamic Acid for bleaching and stabilisation processes.
Geographical Consumption Patterns:
- Asia-Pacific: This region, particularly China and India, is the largest and fastest-growing market. Rapid industrialisation, booming manufacturing sectors, and competitive Sulfamic Acid plant capital cost due to lower manufacturing expenses (labour, raw materials) make it a hub for both production and consumption.
- North America and Europe: Market demand is driven by established industrial cleaning practices, specialised chemical production, and adherence to strict environmental and safety regulations, which favour Sulfamic Acid's properties.
- Latin America, the Middle East, and Africa: These regions are experiencing increasing industrial activity and infrastructure development, resulting in a rising demand for industrial cleaners and chemical intermediates.
- Regulatory Environment: Stricter environmental and safety regulations globally promote the use of less hazardous chemicals. Sulfamic Acid's comparatively lower corrosiveness and toxicity make it a preferred choice, indirectly driving its market growth and influencing technology implementation costs for alternative cleaning agents.
- Focus on Cost-Efficiency and Maintenance: Industries are increasingly prioritising preventative maintenance and efficient cleaning to extend equipment lifespan and minimise downtime. The effectiveness of sulfamic acid in descaling further drives its demand, which in turn impacts its procurement decisions.
Capital Expenditure (CAPEX) for a Sulfamic Acid Manufacturing Plant
The CAPEX for a Sulfamic Acid plant capital cost involves significant initial capital investment costs for acquiring land, construction, and specialised equipment required for the manufacturing process. A robust Sulfamic Acid manufacturing plant cost breakdown includes:
- Raw Material Storage and Handling:
- Storage Tanks/Silos: For liquid urea solution, liquid sulfur trioxide (or storage for oleum, from which SO3 is derived), and concentrated sulfuric acid. These require specialised corrosion-resistant materials.
- Pumps and Piping: strong pump and piping networks for transferring liquid raw materials to reaction vessels.
- Weighing and Dosing Systems: Accurate systems for measuring and feeding precise quantities of each feedstock into the reactors.
- Reaction Section:
- Primary Reactor (for reacting Urea with Sulfur Trioxide): A stirred tank reactor, potentially jacketed for temperature control, designed to handle the exothermic reaction between urea and sulfur trioxide to form the intermediate sulfonic acid group-containing compound. Materials of construction must resist strong acids.
- Secondary Reactor (for reacting Intermediate with Sulfuric Acid): Another stirred tank reactor where the intermediate reacts with sulfuric acid. This vessel also requires robust construction and precise temperature control, potentially with reflux capabilities to manage byproduct gases.
- Reflux Condensers: For condensing and returning sulfuryl chloride or other solvent vapours (if used in certain processes for temperature control or as a reaction medium) back to the reactor, enhancing production efficiency metrics.
- Gas Scrubber/CO2 Treatment: Equipment to handle the carbon dioxide byproduct, possibly including a scrubber to remove any acidic fumes before emission.
Separation and Purification Section:
- Crystallisers: For the controlled crystallisation of Sulfamic Acid from the reaction mixture. It may involve cooling crystallisers or agitated tank crystallisers.
- Centrifuges/Filters: Solid-liquid separation equipment (e.g., pusher centrifuges, basket centrifuges, or vacuum filters) to separate the Sulfamic Acid crystals from the mother liquor.
- Dryers: Rotary dryers, fluid bed dryers, or vacuum dryers to reduce the moisture content of the Sulfamic Acid crystals to specification.
- Utilities and Ancillary Systems:
- Chillers/Cooling Water System: For maintaining exothermic reaction temperatures and cooling during crystallisation.
- Steam Generation System: Boilers for providing heat to certain process steps (e.g., for initial heating, drying).
- De-mineralised Water Plant: For process water requirements.
- Compressed Air System.
- Effluent Treatment Plant (ETP): Essential for treating liquid effluents to comply with environmental regulations, including neutralisation and potentially solid waste handling.
- Control Room and Instrumentation: Advanced Distributed Control Systems (DCS) or Programmable Logic Controllers (PLCs) with sensors, transmitters, and control valves for automated process monitoring and control.
- Packaging and Warehousing: Equipment for packaging the final product (e.g., bagging machines) and storage facilities.
- Land and Civil Construction: Costs associated with acquiring land and constructing industrial buildings, foundations, and support structures.
- Technology Licensing Fees: Payments to the technology provider for access to proprietary process designs.
Operating Expenses (OPEX) for Sulfamic Acid Manufacturing
- Operating expenses (OPEX) are the recurring manufacturing expenses necessary for sustaining production and managing daily operations. These ongoing expenses contribute directly to production cost analysis and influence operational cash flow.
- Raw Material Costs: The largest component of OPEX, including the procurement costs of urea, sulfur trioxide (or its precursor sulfur), and sulfuric acid. The market price fluctuations of these key feedstock materials can significantly impact overall manufacturing expenses.
- Energy Costs: Substantial electricity consumption for pumps, agitators, centrifuges, dryers, and cooling systems. Thermal energy for heating and evaporation. Energy efficiency is a key area for cost structure optimisation.
- Labour Costs: Wages, salaries, and benefits for plant operators, maintenance personnel, quality control staff, and administrative support.
- Utilities: Water consumption, steam, compressed air, and the costs associated with effluent treatment and waste disposal.
- Maintenance and Repairs: Routine maintenance, preventative maintenance programs, and unforeseen repair costs for all plant equipment.
- Consumables: Costs for filter media, reagents used in purification, and other process aids.
- Packaging Costs: Material costs for bags, containers, and labels.
- Depreciation and Amortisation: Non-cash expenses reflecting the wear and tear of CAPEX assets and the amortisation of intangible assets like technology licensing fees.
- Overhead Costs: General administrative expenses, insurance, property taxes, and other indirect costs.
- Logistics and Transportation: Costs for transporting raw materials to the plant and distributing the final Sulfamic Acid product to customers. Supply chain optimisation efforts can significantly reduce these fixed and variable costs.
- Environmental Compliance Costs: Expenses related to emissions monitoring, wastewater treatment, and solid waste management, ensuring adherence to environmental regulations.
Effective lifecycle cost analysis involves careful management of both CAPEX and OPEX to ensure a competitive cost of production and maximum return on investment (ROI).
Manufacturing Process:
This report comprises a thorough value chain evaluation for Sulfamic Acid manufacturing and consists of an in-depth production cost analysis revolving around industrial Sulfamic Acid manufacturing.
- Production from Urea and Sulfur Trioxide: The feedstock required for this process includes Urea, Sulfur Trioxide, and Sulfuric Acid.
The production of sulfamic acid from urea, sulfur trioxide, and sulfuric acid is carried out in two main steps. As the first step, urea is reacted with sulfur trioxide, resulting in the formation of an intermediate compound that incorporates a sulfonic acid group. Then, the obtained intermediate is treated with sulfuric acid, which leads to the formation of sulfamic acid as the final product, while carbon dioxide is released as a byproduct.
Sulfamic Acid is also known as amidosulfonic acid or sulfamidic acid. It is a unique inorganic acid with a set of properties that distinguish it from common mineral acids and contribute to its widespread industrial applications.
- Chemical Formula: H3NSO3
- Molecular Weight3 97.09 g/mol
- Appearance: White crystalline solid or powder.
- Odor: Odorless.
- Solubility: It is highly soluble in water and forms strongly acidic solutions. Its solubility in water is approximately 213 g/L at 20 degree Celsius. It is slightly soluble in methanol and insoluble in ethanol, ether, carbon disulfide, and liquid sulfur dioxide.
- Melting Point: Its melting point is around 205-209 degree Celsius. It decomposes upon melting, while producing sulfur trioxide, sulfur dioxide, nitrogen, hydrogen, and water at higher temperatures (above 260 degree Celsius).
- Density: Approximately 2.151 g/cm³ at 25 degree Celsius.
- pH: A 10 g/L aqueous solution has a pH of 1.2, which indicates its strong acidic nature.
- Non-Hygroscopic: Sulfamic Acid is non-hygroscopic, meaning it does not readily absorb moisture from the air, which makes it easier to handle and store.
- Low Corrosiveness: Its corrosiveness to metals is significantly lower than that of hydrochloric acid, especially when used with appropriate inhibitors, which makes it ideal for cleaning metal equipment.
- Non-Volatile: It is a non-volatile solid, which reduces fuming and hazards associated with handling strong liquid acids.
- Toxicity: It has relatively low toxicity compared to other strong mineral acids, though prolonged skin or eye contact should be avoided.
- Reactivity:
- Reacts with metals, metal oxides, carbonates, and hydroxides to form soluble sulfamate salts.
- Reacts with nitrates or nitrites, which is leveraged in dye manufacturing to remove excess nitrites.
- Can react with strong oxidants.
- Stability: Stable under normal storage conditions.
- Form: It is generally sold in the form of a powder or crystals, but can also be supplied as a liquid solution.
All these properties make Sulfamic Acid a preferred choice for various applications where strong acidity is required without the drawbacks of high volatility, corrosiveness, or significant hygroscopicity. Its unique properties also contribute to its robust economic feasibility in the market.
We at Procurement Resource ensure that this report is not only cost-efficient, environmentally sustainable, and aligned with the latest technological advancements but also that you are equipped with all necessary tools to optimise supply chain operations, manage risks effectively, and achieve superior market positioning for Sulfamic acid.
Key Insights and Report Highlights
Report Features |
Details |
Report Title |
Sulfamic Acid Manufacturing Plant Project Report |
Preface |
Overview of the study and its significance. |
Scope and Methodology |
Key Questions Answered, Methodology, Estimations & Assumptions. |
Executive Summary |
Global Market Scenario, Production Cost Summary, Income Projections, Expenditure Projections, Profit Analysis. |
Global Market Insights |
Market Overview, Historical and Forecast (2019-2029), Market Breakup by Segment, Market Breakup by Region, Price Trends (Raw Material Price Trends, Sulfamic Acid Price Trends, Competitive Landscape (Key Players, Profiles of Key Players). |
Detailed Process Flow |
Product Overview, Properties and Applications, Manufacturing Process Flow, Process Details. |
Project Details |
Total Capital Investment, Land and Site Cost, Offsites/Civil Works Cost, Plant Machinery Cost, Auxiliary Equipment Cost, Contingency, Consulting and Engineering Charges, Working Capital. |
Variable Cost Analysis |
Raw Material Specifications, Raw Material Consumption, Raw Material Costs, Utilities Consumption and Costs, Co-product Cost Credit, Labour Requirements and Costs. |
Fixed Cost Analysis |
Plant Repair & Maintenance Cost, Overheads Cost, Insurance Cost, Financing Costs, Depreciation Charges. |
General Sales and Administration Costs |
Costs associated with sales and administration |
Project Economics |
Techno-economic Parameters, Income Projections, Expenditure Projections, Financial Analysis (Payback Period, Net Present Value, Internal Rate of Return), Profit Analysis, Production Cost Summary. |
Report Format |
PDF for BASIC and PREMIUM; PDF+Dynamic Excel for ENTERPRISE. |
Pricing and Purchase Options |
BASIC: USD 2999
PREMIUM: USD 3999
ENTERPRISE: USD 5999 |
Customization Scope |
The report can be customized based on the customer’s requirements. |
Post-Sale Analyst Support |
10-12 Weeks of support post-sale. |
Delivery Format |
PDF and Excel via email; editable versions (PPT/Word) on special request. |
Key Questions Covered in our Sulfamic acid Manufacturing Plant Report
- How can the cost of producing Sulfamic acid be minimised, cash costs reduced, and manufacturing expenses managed efficiently to maximise overall efficiency?
- What is the estimated Sulfamic acid manufacturing plant cost?
- What are the initial investment and capital expenditure requirements for setting up an Sulfamic acid manufacturing plant, and how do these investments affect economic feasibility and ROI?
- How do we select and integrate technology providers to optimise the production process of Sulfamic acid, and what are the associated implementation costs?
- How can operational cash flow be managed, and what strategies are recommended to balance fixed and variable costs during the operational phase of Sulfamic acid manufacturing?
- How do market price fluctuations impact the profitability and cost per metric ton (USD/MT) for Sulfamic acid, and what pricing strategy adjustments are necessary?
- What are the lifecycle costs and break-even points for Sulfamic acid manufacturing, and which production efficiency metrics are critical for success?
- What strategies are in place to optimise the supply chain and manage inventory, ensuring regulatory compliance and minimising energy consumption costs?
- How can labour efficiency be optimised, and what measures are in place to enhance quality control and minimise material waste?
- What are the logistics and distribution costs, what financial and environmental risks are associated with entering new markets, and how can these be mitigated?
- What are the costs and benefits associated with technology upgrades, modernisation, and protecting intellectual property in Sulfamic acid manufacturing?
- What types of insurance are required, and what are the comprehensive risk mitigation costs for Sulfamic acid manufacturing?
1 Preface
2 Scope and Methodology
2.1 Key Questions Answered
2.2 Methodology
2.3 Estimations & Assumptions
3 Executive Summary
3.1 Global Market Scenario
3.2 Production Cost Summary
3.3 Income Projections
3.4 Expenditure Projections
3.5 Profit Analysis
4 Global Sulfamic Acid Market
4.1 Market Overview
4.2 Historical and Forecast (2019-2029)
4.3 Market Breakup by Segment
4.4 Market Breakup by Region
4.6 Price Trends
4.6.1 Raw Material Price Trends
4.6.2 Sulfamic Acid Price Trends
4.7 Competitive Landscape
4.8.1 Key Players
4.8.2 Profiles of Key Players
5 Detailed Process Flow
5.1 Product Overview
5.2 Properties and Applications
5.3 Manufacturing Process Flow
5.4 Process Details
6 Project Details, Requirements and Costs Involved
6.1 Total Capital Investment
6.2 Land and Site Cost
6.3 Offsites/ Civil Works Cost
6.4 Plant Machinery Cost
6.5 Auxiliary Equipment Cost
6.6 Contingency, Consulting and Engineering Charges
6.6 Working Capital
7 Variable Cost Analysis
7.1 Raw Materials
7.1.1 Raw Material Specifications
7.1.2 Raw Material Consumption
7.1.3 Raw Material Costs
7.2 Utilities Consumption and Costs
7.3 Co-product Cost Credit
7.4 Labour Requirements and Costs
8 Fixed Cost Analysis
8.1 Plant Repair & Maintanence Cost
8.2 Overheads Cost
8.3 Insurance Cost
8.4 Financing Costs
8.5 Depreciation Charges
9 General Sales and Administration Costs
10 Project Economics
10.1 Techno-economic Parameters
10.2 Income Projections
10.3 Expenditure Projections
10.4 Financial Analysis
10.5 Profit Analysis
10.5.1 Payback Period
10.5.2 Net Present Value
10.5.3 Internal Rate of Return
11 References