The Food-Grade Phosphoric Acid Unit Operated by GACL in Dahej, Gujarat has been Commissioned
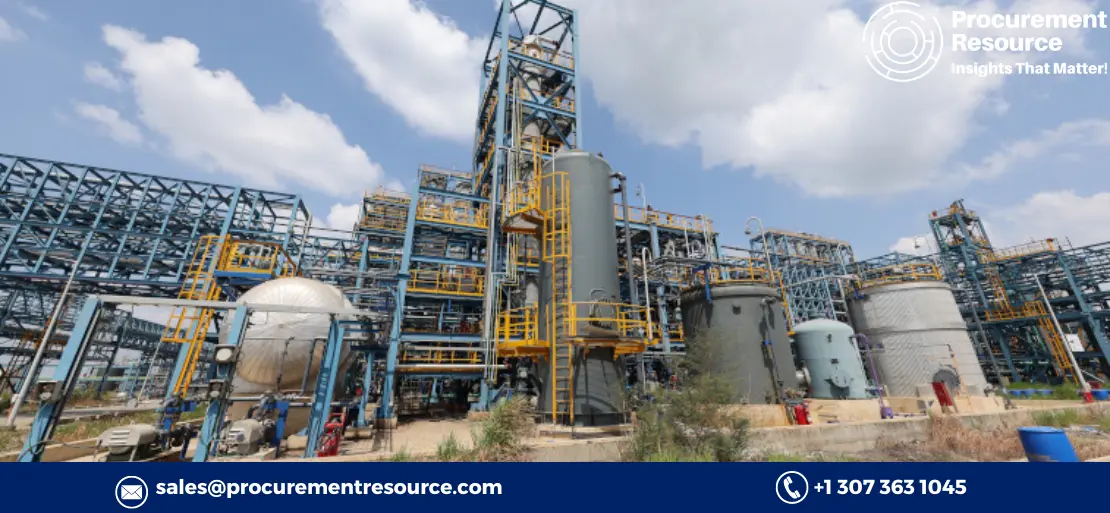
Gujarat Alkalies and Chemicals Limited (GACL) is one of India's major caustic soda producers, having a capacity of 1,087 tonnes per day (TPD). GACL's new phosphoric acid facility is scheduled to open in February 2023.
The phosphoric acid factory is currently 90.2 percent complete. The plant's capital expenditure is Rs. 520 crores. Caustic soda with a coal-fired power plant (a partnership with NALCO) has recently been commissioned and is being stabilised.
The facility has an 800 TPD capacity. Unit two is scheduled to be completed in January 2023. The entire project cost for both units one and two is Rs. 2,300 crores.
The Dahej Chlorotoluene Project's coal-fired power plant has been halted. The power plant would cost Rs. 325 crore and have a capacity of 65 MW.
The Dahej chlorotoluene project, with a capacity of 90 TPD, would cost Rs. 350 crore, and basic engineering work for the plant is already underway.
Request Access For the Latest Price Trends of Phosphoric Acid
GACL operates three facilities in Vadodara, Dahej-I, and Dahej-II. Caustic soda group, caustic potash group, hydrogen peroxide, chloromethanes, and poly aluminium chloride are the major products in Vadodara.
Caustic soda group, hydrogen peroxide, phosphoric acid, anhydrous aluminium chloride, poly aluminium chloride, sodium chlorate, stable bleaching powder, chloromethanes, and hydrazine hydrate are major products in Dahej.
About the Company
Gujarat Alkalies and Chemicals Limited (GACL) is an Indian chemical manufacturing firm situated in Vadodara. The company was founded in 1973 with the intention of producing caustic soda and other basic chemicals. GACL has diversified its product line over the years and now manufactures a wide range of chemicals, including chlorine, hydrogen peroxide, and several specialised chemicals.
It is a public corporation that trades on the Bombay Stock Exchange and the National Stock Exchange of India. The company is committed to environmental stewardship and sustainability, and it has developed a number of efforts to reduce its environmental effect and conserve natural resources.
Price Trend and Forecast
North America
Phosphoric Acid prices have recently fallen in the North American region. The downward trend was sustained this quarter due to weakened market dynamics and poor demand from both domestic and international markets.
Furthermore, downstream industries, particularly fertilisers, took a wait-and-see attitude towards the price trend, resulting in weak purchasing activity. According to market participants, operating rates in the US domestic market remained low.
The deterioration in operating conditions was mostly caused by further reductions in output and new orders. However, sticky inflation pushed the US Federal Reserve to raise interest rates, affecting consumer confidence, and traders made offtakes at lower margins amid ample supply.
Asia Pacific
Phosphoric acid prices in the Asia-Pacific area have recently shown a mixed pattern. The Phosphoric Acid market began on a high note, due to an increase in raw material yellow phosphorus prices. Market participants report a revival in market activity following the government's abandonment of its zero-COVID policy.
With a resurgence in demand from downstream fertilisers, food, and other industries ahead of the Lunar New Year break, there were few new orders.
Phosphoric acid manufacturing plants had lower production costs because of a drop in feedstock Yellow phosphorous prices. In terms of supply, inventories in the domestic market were ample following the improvement in industrial operations in China.
Europe
The European Phosphoric Acid market received a pessimistic mood. Phosphoric acid prices in Germany fell during the third quarter due to ample product availability and decreased demand in both the domestic and international markets.
According to market participants, operating rates gradually decreased due to low consumption and no new orders of Phosphoric Acid, but material availability in the local market was unaffected and remained adequate among domestic suppliers as imports from the overseas market remained steady with no supply chain disruption.
Read More About Phosphoric Acid Production Cost Reports - Get Free Sample Copy in PDF
Because buyers lacked confidence, suppliers lowered their quotations to stimulate buying performance.
As per Procurement Resource, Gujarat Alkalies and Chemicals Limited is a large producer of caustic soda in India, with a capacity of 1,087 tonnes per day (TPD). The new phosphoric acid facility at GACL is set to open in February 2023. The phosphoric acid plant is currently 90.2 percent finished.
The capital expenditure for the plant is Rs. 520 crores. Caustic soda production using a coal-fired power plant (a collaboration with NALCO) has recently begun and is being stabilised. The facility can handle 800 TPD. Unit two is expected to be finished in January 2023. The total cost of the project for both units one and two is Rs. 2,300 crores.